Non-contact vibration measurement of highly stressed blade integrated disks (BLISKS)
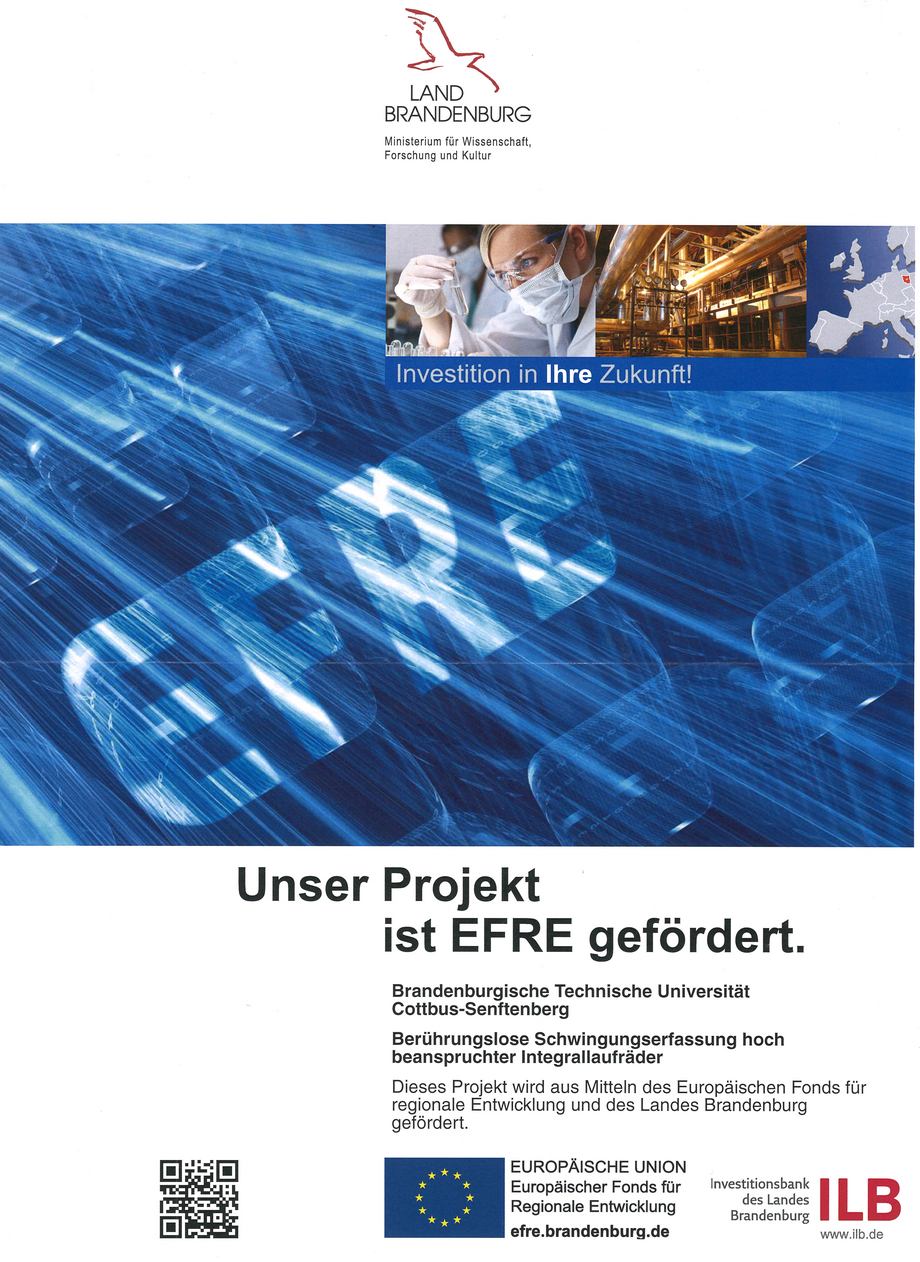
In recent years, the demand for ever more environmentally friendly and efficient turbomachinery that is optimized in terms of fuel consumption and service life has resulted in an increasing number of lightweight construction solutions. In current gas turbine and engine development programs, for example, axial compressor and turbine runners or, in the automotive sector, radial turbine runners of exhaust gas turbochargers are increasingly being manufactured integrally, i.e. as a single component (blisk = blade integrated disk), instead of the usual separate design of blades and disks. In addition to the advantage of reducing the mass, the efficiency of the turbomachine can be improved, for example by allowing higher rotational speeds. The use of this design will also be important in future propulsion systems, which will increasingly focus on hybrid technology or hydrogen combustion.
A consequence of the lightweight blisk design is a higher sensitivity to vibration excitation during operation because the additional damping of the connection between disk and blade is missing. This greater sensitivity usually has a negative influence on the service life of the components. This is further reinforced when the influence of production-related imperfections, which give the individual blades different mechanical properties and are known as blade mistuning, is taken into account. Depending on their distribution, these imperfections sometimes cause a dramatic increase in vibration responses and consequently a reduction in service life. Early identification of vibration problems on the basis of measurements of the mistuning distribution therefore contributes significantly to improving the structural-dynamic understanding of the impellers.
The overall objective of this project is therefore to enable an advanced structural-mechanical and, above all, structural-dynamic evaluation of the vibration behavior of real compressor and turbine blades with respect to tolerances in production or deliberately induced differences. The simulation models required for this purpose are based on highly precise data obtained from vibration measurements and thus allow much more precise predictions to be made, for example, about the service life of a blade.