KoHard - Coaxial laser beam hardening of bores
R&D cooperation project "KoHard - Coaxial laser hardening of bores: Development of a model-based and controlled surface hardening process for bore interiors"
R&D subproject BTU "Development of the computer-aided simulation tool".
Project executing agency: AiF Projekt GmbH, ZIM funding program of the BMWi Duration: 07/2019 to 06/2021
Motivation and goal
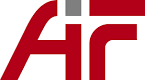
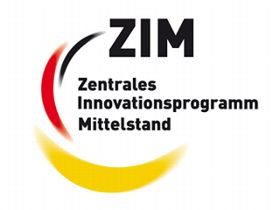
According to the current international state of the art, there is no suitable one-sided technology for laser hardening of complex blind bore profiles with small diameters. The intended laser hardening technology should therefore close the existing gap, based on a reproducible hardening process, and thus enable the cost-effective and efficient implementation of hardened bores.
The aim of this project is the development of a simulation-based laser hardening process based on laser processing optics for the one-sided surface hardening of bores with small diameters of d = 5 - 15 mm and complex bore profiles, characterized by varying bore diameters along the bore axis, transitions between different bore diameters, and the feature of through and blind bores. The approach presented in this project, for which a patent application has been filed and for which the grant decision of the DPMA is available as of 26/11/2018, is based on the use of a small angle between the laser beam and the inside of the bore without the use of mirrors. The challenge is both the development of an appropriate laser optics for universal hardening of bores and the corresponding process design, control or regulation to ensure reproducible and uniform hardening profiles for complex bore profiles with varying diameters along the bore axis as well as variable thermal conductivity ratios.
For the implementation, a model-based and boundary layer hardening process for bores is developed, which combines new technological components (processing optics, sensor technology, control circuits) as well as calculation software for the design of the hardening process and, following the project, is further developed into a fully automated or self-regulating process. An interface between a simulation tool and the processing optics is to transmit control variables with a high degree of automation to the system technology, depending on the calculation results, in order to provide locally adapted process parameters for uniform hardening profiles. Depending on the calculated heat input and geometry-related heat dissipation, the tool provides the maximum temperatures at the surface as a controlled variable of the temperature control loop as well as the corresponding feed rates, in order to achieve geometry-independent equal hardness values at all positions along the bore axis without the previously unavoidable irregularities.
The overall objective of the project is the transfer of the desired technical functionalities into a stable, functionally reliable system suitable for large-scale production. The project is being worked on in two closely interlinked subprojects. Their common goal is to provide an overall solution consisting of processing optics, validated process parameters and simulation-based parameter control for future end users of laser-based hole hardening.
Research partner | Industry partner |
---|---|
BTU Cottbus-Senftenberg, represented byChair of Joining and Welding Technology (Faculty 3) Panta Rhei Halle Konrad-Wachsmann-Allee 17 03046 Cottbus Contact: Dipl.-Ing. Anton Evdokimov | Scansonic IPT GmbHSchwarze-Pumpe-Weg 16 12681 Berlin |