ERDF European Regional Development Fund
The following projects are supported by ERDF funds. The Department of Joining and Welding Technology would like to thank the funding body for the opportunity to implement the research projects.
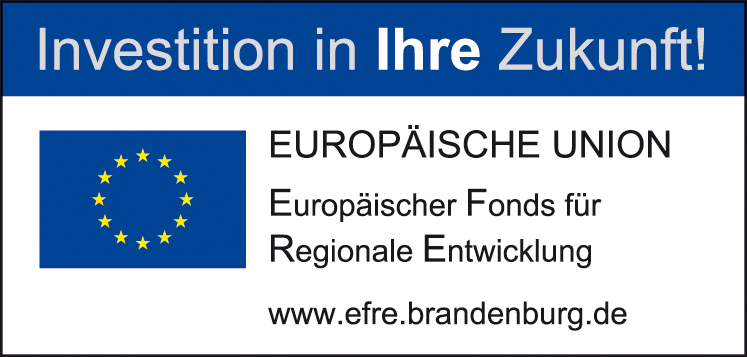
Gas analysis in the material and production chain of additively manufactured, joined and repaired high-performance components for energy and transportation technology
The project will introduce a gas analysis system for hydrogen, oxygen and nitrogen in the process chain of joining, additive manufacturing and repair. The project aims to expand the technical limits of the manufacturing processes and at the same time increase the quality efficiency and sustainability of the materials. Knowledge of the gas concentrations in materials is crucial for the design and optimization of properties and adapted processing.
Green laser as an efficient tool for resource-saving technologies - Green to Green
Within the proposed project, the existing area of laser technology at the Chair of Joining and Welding Technology at the BTU is to be expanded with a green laser in order to be able to process highly reflective materials such as copper and bronze alloys for functional components with a primary focus on electromobility and energy generation. The focus of the research is on new development or transfer of electrically conductive functional components made of copper alloys and the simulation of the entire process chain. In addition to functional integration, another major focus is on the continuous implementation of lightweight construction concepts, taking functionality into account.
Expansion of a simulation and testing center for generate, joining and repair of high-efficiency materials - HighMatPro
Due to increasingly complex alloy compositions, microstructures and manufacturing processes, considerable challenges arise for the processing of high-performance materials, especially in thermomechanical processes such as joining, generating, coating and repairing. The Gleeble 3500 simulation and testing center operated at the Chair of Joining and Welding Technology at the BTU Cottbus-Senftenberg enables processing operations to be researched in a special quality. The system offers the possibility of high-precision physical simulation of thermal and mechanical processes on defined specimens. Findings from laboratory tests can thus be transferred directly to manufacturing processes. As part of the ERDF funding, the simulation and testing center for the investigation of high-performance materials in energy and transport systems will be equipped for the future. To this end, the center is being expanded with non-contact measurement technology for temperature and strain determination. The sensor technology and measurement data acquisition integrated in a closed control loop will form the basis for the exact simulation of the characteristic features of modern processing operations.
smart nanoCOOLing - Development of highly effective smart heat sinks based on nanomodified material systems for the e-mobility of the future
High-performance electronic components form the core elements of an increasingly digitalized energy technology and especially in electromobility. Their functional efficiency will become increasingly important in the coming years. The component properties have a significant influence on the losses during the conversion of electrical energy and the heat generated in the process. The presented project aims at the production of ultra-efficient heat sinks with high thermal and mechanical load capacity. By combining additive manufacturing for the implementation of complex, internal cooling structures and stressable, nano-reinforced material systems with the highest thermal conductivity, a new class of heat sinks is to be designed and realized suitable for series production.
i-flow - Efficiency increase of solid oxide fuel cells by infiltration and optimization of flow characteristics
The aim of this research project is to increase the efficiency of high-temperature fuel cells (SOFC). By local infiltration of the individual cells, which are made of ceramic and metallic materials, the electrical and thermal contacting is to be improved with minimal influence on the gas diffusion and flow, and the mechanical stress on the anode and cathode in the contact area is to be reduced. A geometric optimization of the cell-connecting metallic bipolar plates, which ensure a separation and flow of the process gases hydrogen and oxygen, should also contribute to an increase in efficiency compared to conventional SOFCs. Complex geometries are made possible by the use of additive manufacturing processes, such as selective laser melting. | Poster
mediStent - Additive manufacturing of medical coronary stents for the treatment of arteriosclerosis
The aim of the research project is to develop additively manufactured stents for use as medical implants, the required materials and the associated system and testing technologies for efficient and resource-saving production. For this purpose, the 3D printing processes selective laser melting (SLM®) and the fused deposition modeling process (FDM) are being further developed for the implementation of filigree, complex stent structures with mechanical properties that meet the requirements. The range of applications in medical technology is being expanded through the production of new types of metal powder by atomization and special polymer-bound metal filaments by compounding. The targeted design of the additive manufacturing processes, a requirement-oriented specification of the sintering process and a further development of the electrochemical polishing enable the defined adjustment of the mechanical properties and the implementation of highly filigree stent structures.
Material- and resource-efficient process chains through combination of forming processes and additive manufacturing
The main objective of the planned project is to develop efficient process chains by combining forming and additive manufacturing processes in order to economically produce large-volume components with complex geometries in small series or as individual parts. The process combinations allow the resource-saving production of highly stressed components, whose dimensions are not limited by the restrictions of additive manufacturing, due to the summation of the respective technological advantages. | Poster
The research project focuses on the following research topics:
- Experimental investigations on the integration of additive manufacturing processes, in particular laser cladding, into forming process chains.
- Numerical process simulation of the laser cladding process
- As well as the production of demonstrators
Resource-efficient lightweight construction from metallic materials by generative, selective laser beam melting
Within the project, materials and manufacturing research at the BTU Cottbus - Senftenberg is to be expanded to include the innovative and forward-looking process of selective laser beam melting. The process is one of the powder bed based generative processes, with which very complex and filigree structures with minimal wall thicknesses and very good surface qualities can be produced without tools. Complex lightweight structures, which in most cases have three-dimensional structures (e.g. lattice, structured thin-walled and macroporous structures), have great potential and a wide range of applications, such as for vehicle, machine and energy plant construction and also for energy technology apparatus (catalytic converters, heat exchangers and reactors). The developments address requirements with regard to complex, functionally integrated, weight-optimized lightweight solutions made of metallic materials.
Fabrication and joining of energy-efficient hybrid fiber-plastic/metal multilayer composites
A new generation of lightweight semi-finished products combines thin thermoplastic layers and metallic individual layers to form a hybrid multilayer composite with outstanding manufacturing and system properties. They represent a promising alternative for vehicle construction. In particular, the relatively young material group of textile-reinforced thermoplastics offers significant advantages for use in hybrid multilayer composites, which is mainly due to the short cycle times in component manufacture and the use of cost-effective thermoplastic systems.
The aim of the project is therefore to design an efficient production and processing of hybrid FRP/M multilayer composite semi-finished products, which creates the conditions for their use in large-scale production.