Substitution of metallic thrust fields in vehicle construction through joining integration of FKV shells (CMT-PIN)
Research Association: Research Association on Welding and Allied Processes of the DVS
Project executing agency: AiF Projekt GmbH, IGF funding programme of the BMWi Duration: 01.12.2019 - 30.11.2021

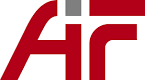
Research Goal
Development of a novel joining process for mixed joints in order to integrate shear fields made of FRP into metallic structures. As a primary goal, the joints should exhibit force-flow-compatible and high-strength connection properties by non-destructively retaining the fibers in the FRP.
Motivation and goal
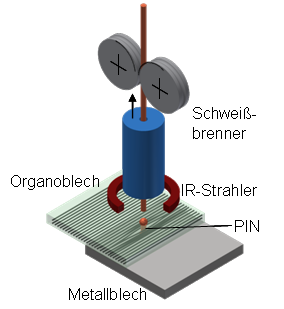
In recent years, an integrated overall approach to lightweight materials, production and mould design has become established in vehicle construction. Increasing demands on comfort and driving safety as well as alternative drive concepts have nevertheless led to an increase in the average total weight of vehicles. Lightweight solutions for vehicle bodies, which account for about 40 % of the total weight of an average passenger car, are particularly important for the desired weight reduction. The structural use of fiber-reinforced plastic (FRP) composites in combination with high-strength steel alloys allows high-quality weight-optimized car bodies to be implemented in mixed construction. Furthermore, shear panels are recognized as a design principle of lightweight construction, whereby circumferential frame profiles are usually filled by sheet metal panels. With highly loadable joints for FRP/metal mixed joints, the shear field concept can be ideally implemented with a simultaneous significant reduction in weight, if the forces can be transferred from the metallic structure to the FRP shell in a manner suitable for the material.
Numerous structures are designed in mixed construction with thermoplastic fibre composites, in which metallic components have been substituted by fibre-reinforced thermoplastics. Examples of this are mainly kmU-manufactured front ends, seat shells or door impact beams made of FRP.
The increased use of highly anisotropic fiber reinforced composites and their specific requirements for force transmission are currently directing the focus increasingly towards joining technology, which as an important component of holistic FRP/metal composite designs has received too little attention in the past [1]. According to the current state of the art, the mechanical joining technique leads to structural damage in the FRP, for example through holes drilled by machining for blind rivets, screws, lockbolts or by setting punch rivets. As a result of the interrupted force flow (severed fibers), failure-critical excess notch stresses are induced at the joint. In addition to other disadvantages, when using the currently known joining methods, the FKV components generally have to be designed thicker and with greatly oversized connecting flanges than theoretically necessary as a result of the machining of bores. This circumstance requires the provision of new reliable efficient solutions in the field of joining technology. An optimal connection should not only be easy to implement, but also not interrupt the force flow in the FRP component and limit the increase in mass and installation space to a minimum. The development of an efficient, robust and automatable joining technique for mixed construction methods with metals and thermoplastic FRP is therefore currently in the focus of many O-EM's, suppliers and service companies and is therefore the goal of the project.
The following open questions are to be answered by the project:
- What are the suitable process parameter windows for different organic sheet thicknesses?
- What is the effect of heating on the FKV? How should the temperature-time regimes be designed for optimum heating with minimum impairment of the FRP? What decomposition products, if any, can be formed and in what quantities?
- How must the joining zones be designed (pin spacing, edge spacing, number of pins, single-row and multi-row design, pin head diameter) in order to achieve optimum utilization of the sheet metal strength?
- What strengths can be achieved in combination with bonding? How much is the adhesive affected during the heating and welding process?
- What is the corrosion resistance of the CMT-PIN joints?
Benefits for SMEs
A direct kmU-compatible implementation of the joining of FRP with metals is made possible by using conventional and cost-effective metal inert gas welding technology, which is well known to the processors of traditional metallic construction methods. For the users, a directly exploitable economic benefit results from the implementation of the new joining technology:
- Creation of a global unique selling point in the field of key lightweight construction technology.
- Low investment costs for the conversion of existing systems
- Low maintenance and repair costs
- Low energy and assembly costs
- High material and raw material efficiency and resulting mass savings
- Low risks due to the use of proven standard processes
- Securing/creation of jobs
- Development of new strategic business areas
- Development of new sales markets
Results
The current processing status can be found under the following link:
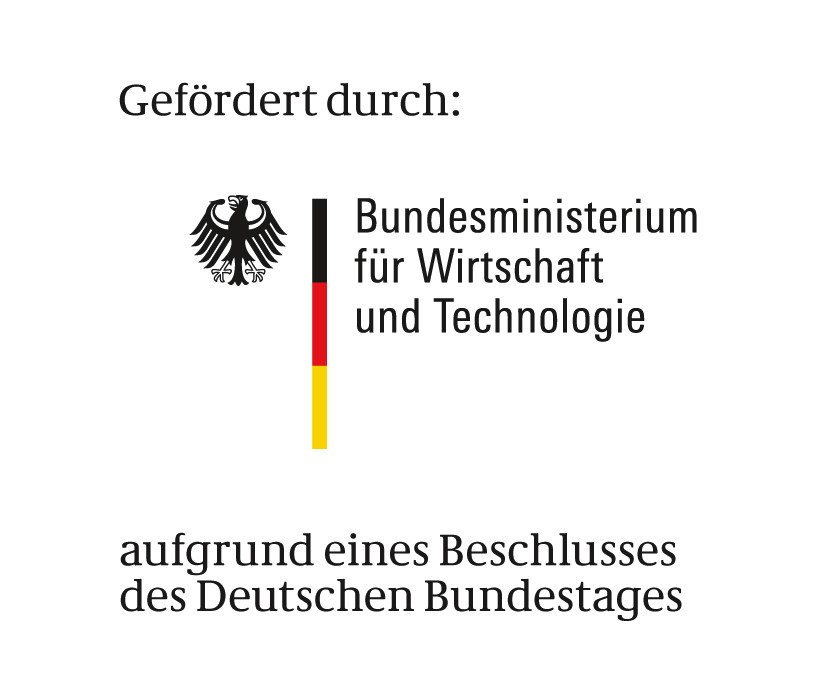
Acknowledgements
The research project with the IGF no. 20649 BR of the AiF research association "DVS - Deutscher Verband für Schweißen und verwandte Verfahren e. V." is funded within the framework of the programme for the promotion of joint industrial research and development (IGF) by the BMWi on the basis of a resolution of the German Bundestag.