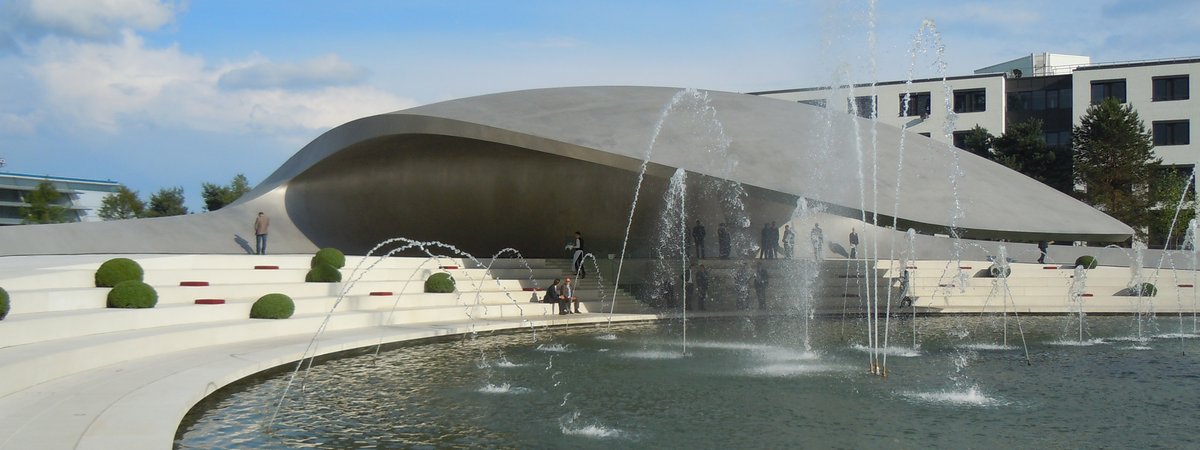
The consideration of welding influences on steel formwork structures
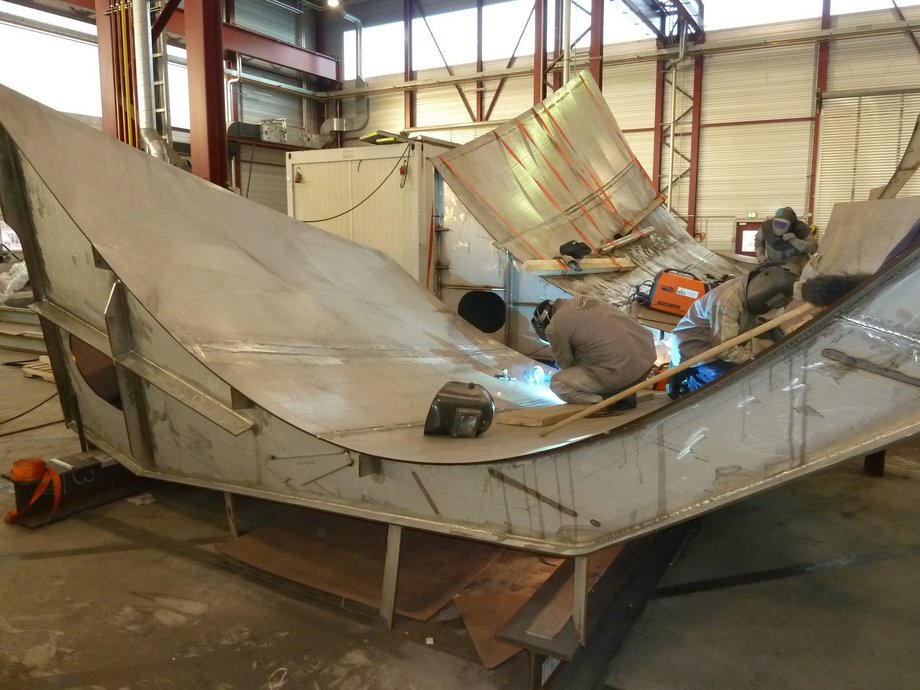
Reinforced formwork structures (monocoque) facilitate exceptionally efficient and material-minimised steel structures. The calculation of these structures is currently proving an issue for engineers. Welding distortions and residual welding stresses generate imperfections which can only be translated with difficulty into a reliable simulation model. In the project »Determination of the load capacity of innovative steel formwork structures under realistic consideration of welding distortions« funded by the Arbeitsgemeinschaft industrieller Forschungsvereinigungen (Federation of Industrial Cooperative Research Associations AiF) with 517,720.00 Euros, the Chairs of Steel and timber construction and Joining and welding technology are working on a reliable calculation model. Numerous production companies, engineering offices and software developers are participating in the project.
On reinforced formwork structures, the supporting structure consists of a thin outer skin, and if applicable also an inner skin. Using methods familiar from ship construction, the metal sheets can be bent double as required. This results in economically viable but also complex constructions. The metal sheets are reinforced to provide shape and reinforcement against bulging due to ribs and transverse bulkheads. The quantity of reinforcements plays a major role in determining the amount of material and production expenses.
Today, planning is mainly conducted on the computer with the aid of the finite element method. Here a geometric and material non-linear analysis, taking into account imperfections (GMNIA) possesses the highest achievable theoretical degree of reality. Imperfections are to be understood as deviations on the ideal geometry and the material, which always occur during welding in the form of welding distortions and residual welding stresses.
The quality of such a numerically-supported verification is particularly dependent on the imperfection assumptions introduced into the simulation model. A direct numeric calculation through GMNIA frequently fails due to the fact that imperfections in general are unknown parameters. They are unknown because the forms thus realised are always new. Only conservative standardisation has therefore been possible up to now. In construction practice, this takes place with the aid of simplified calculation procedures, which are based on so-called bulge reduction curves. Here the verifications are in part too conservative, as they also have to cover the worst case.
The welding simulation offers the possibility of direct calculational forecasting of welding influences. In the industry, this method is used for smaller components or components in series production. For the component sizes typical in steel construction (and the related larger calculation times), the application of classic welding simulation methods is not possible in the foreseeable future. The so-called hybrid model developed at the BTU has recently offered a practice-relevant method regarding welding simulations for larger components. From a dimensioning point of view, an interface should be realised using this model and ensured in appropriate real tests on small part samples. The objective is to develop a method which in future permits the more reliable application of GMNIA calculations.