VIT-V - Verfahren der Industrie 4.0 für die Triebwerks-Vorentwicklung (Industry 4.0 processes for engine predevelopment)
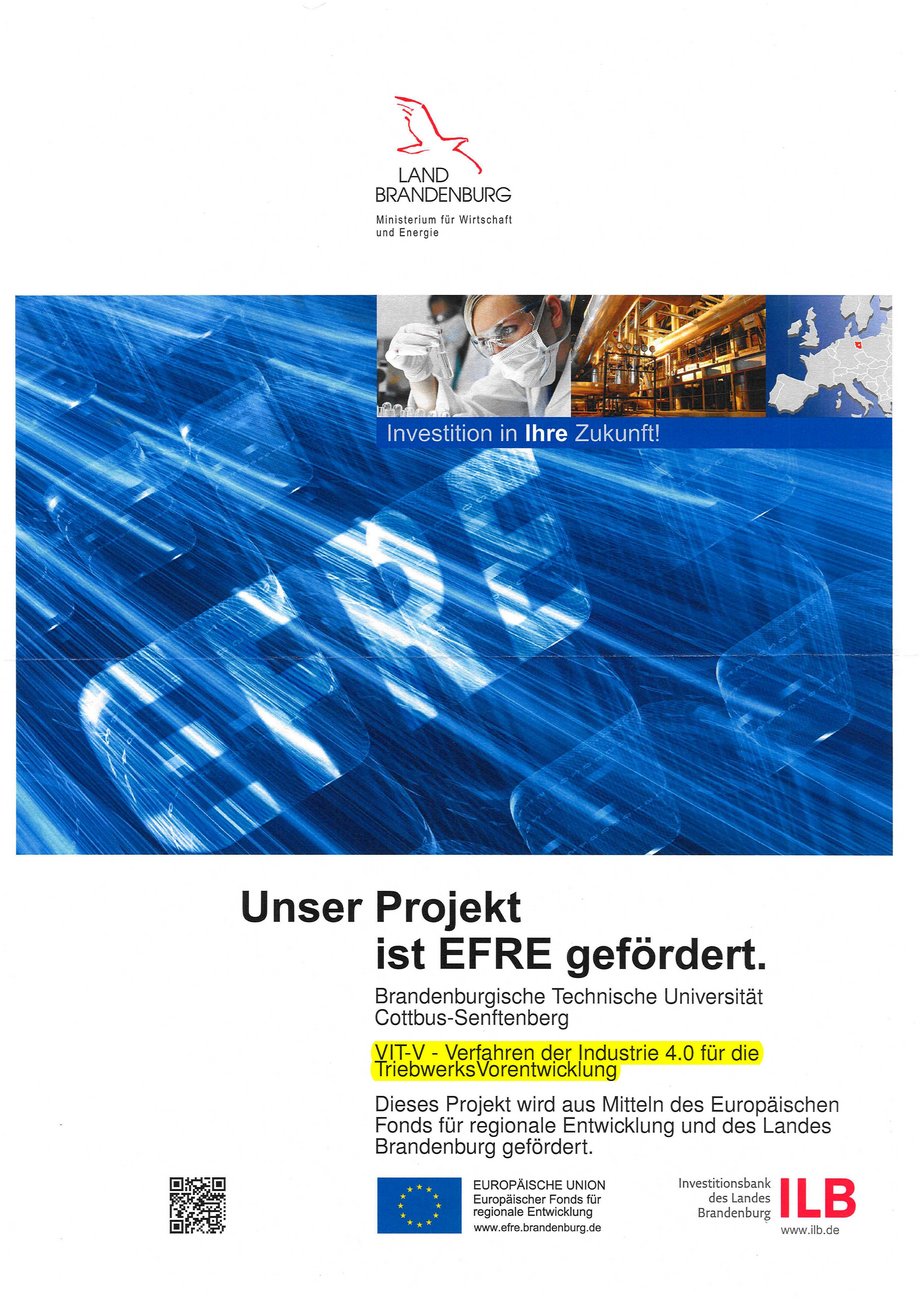
- Funding: approx. 3 million €
- Duration: 7/2018 - 6/2021
The acronym VIT-V stands on the one hand for the topic (see above), and on the other hand as the interpretation VIT-5 for the continuation of a series of successful research projects carried out together with Rolls-Royce Germany on the topic of "Virtual Engine". The success story began in 2003 with the LuFo pilot project VIT, in which it was demonstrated that numerical optimisation methods need not be limited to academic issues, but can also effectively support the development of systems as complex as engines. Within the framework of the subsequent VIT-2 to VITIV projects, highly developed analysis and design processes were developed with which engines can be made even more efficient in order to reduce fuel consumption and emissions. The aim of the current project is to develop new types of design processes for engines, in which not only the ideal state of the design is considered, but also changes in engine components due to manufacturing tolerances and in real operation.
In the joint research project with a total volume of 11.5 million euros, both research partners are being funded by the Brandenburg Ministry for Economic Affairs and Energy with almost 3 million euros each from the European Regional Development Fund (ERDF). At the BTU, five chairs are supervising 12 doctoral students and 1 post-doctoral student in 13 themed work packages. In addition, each work package is supervised by Rolls-Royce experts in order to link the academic perspective with the expert knowledge of the engine manufacturer.
Project management | ||
---|---|---|
Excellence for design | Excellence for operation | Excellence for maintenance |
A1 Automatic model generation for engine architecture decisions | B1 Data management and analysis in engine technology | C1 Prozesse zur Ermittlung von In-Service-Lebensdauern |
A2 Methods for the automatic transfer of CAD models to structural analysis | B2 Thermomechanical models for the complete engine under real flight conditions | C2 Networking of integrated simulation and visualisation |
A3 Engine structure models with variable depth of detail | B3 Consideration of operational data in the customer offer for new engines | C3 Cooperative maintenance with support from VR system |
A4 Particle simulation of a bird strike | B4 Robust design of engine blades under consideration of real geometry data | C4 Processes for automated aeroelastic compressor design |
B5 Robust engine design with uncertain operational data |
Professorships involved
Prof. Dr.-Ing. habil. Hon. Prof. (NUST) Dieter Bestle (Project Manager), Chair of Engineering mechanics and vehicle dynamics
apl. Prof. Dr.-Ing. habil. Bernd Beirow, Chair of Structural Mechanics and Vehicle Vibrational Technology
Prof. Dr.-Ing. habil. Christian Hentschel, Chair of Media technology
Prof. Dr.-Ing. Klaus Höschler (UTC Direktor), Chair of Aeroengine Design
Prof. Dr.-Ing. habil. Ingo Schmitt, Chair of Database and information systems