The following projects are supported by ERDF funds. The Department of Lightweight Design with Structured Materials would like to thank the funding agency for the opportunity to realize the research projects.
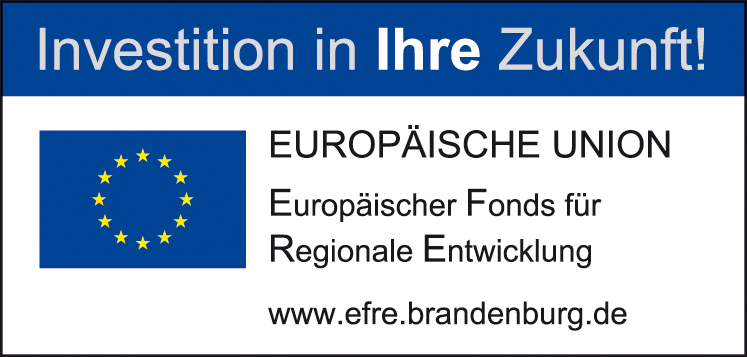
Overcoming boundaries with lightweight technologies Sustainable development of a cross-border competence network for knowledge and technology transfer in the field of application-oriented lightweight construction

Verbundprojektpartner
Chair of Polymer-based Lightweight Design of the BTU Cottbus - Senftenberg - Prof. Holger Seidlitz,
Institute of Mechanical Engineering of the Univeristy of Zielona Góra - Prof. Justyna Patalas-Maliszewska, Prof. Sławomir Kłos
SIMP Branch in Gorzów Wielkopolski - Włodzimierz Fleischer, Ryszard Bartz
Kurzbeschreibung
The aim of the bilateral project is to establish a competence network with actors on both sides of the German-Polish border. In particular, the target groups of students, academic staff and employees are to be addressed. As representatives of the academic institutions and the regional economy, they are to accompany and shape the transfer of knowledge and technology in the field of application-oriented lightweight construction from the universities to the regional companies. The aim is not only to overcome geographical borders, but also to break down linguistic and mental barriers and thus to ensure the continuation of contacts beyond the project. The accelerated and sustainable development of competences in the field of the key technology of lightweight construction represents an opportunity for the upcoming structural change and the region.
Support Framework
Kooperationsprogramm INTERREG VA Brandenburg - Polen 2014-2020
Project period: 01.03.2020 - 30.06.2022
mediStent - Additive manufacturing of medical coronary stents for the treatment of arteriosclerosis
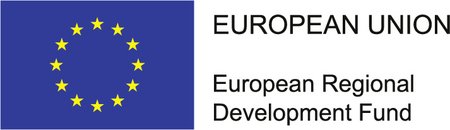
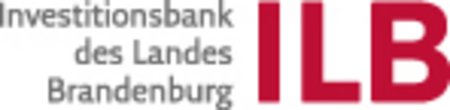
Joint project partners
Chair of Polymer-based Lightweight Design - Prof. Dr.-Ing. Holger Seidlitz,
Chair of Joining and Welding Technology - Prof. Dr.-Ing. Vesselin Michailov
Chair of Metallurgy and Materials Engineering - Prof. Dr.-Ing. habil. Sabine Weiß
Brief description
The aim of the research project is to develop additively manufactured stents for use as medical implants, the required materials and the associated system and test technologies for efficient and resource-saving production. For this purpose, the 3D printing processes SLM and FDM are being further developed for the implementation of filigree, complex stent structures with mechanical properties that meet the requirements. The range of applications in medical technology is expanded through the production of new types of metal powder through atomization and special polymer-bound metal filaments through compounding. The targeted design of the additive manufacturing process, the sintering process and the electrochemical polishing enable the implementation of highly filigree stent structures.
Support Framework
Richtlinie des Ministeriums für Wissenschaft, Forschung und Kultur (MWFK) zur Förderung der „Stärkung der technologischen und anwendungsnahen Forschung an Wissenschaftseinrichtungen im Land Brandenburg“ (StaF-Richtlinie)
Project period: 01.03.2020 - 28.02.2022
Development of a new type of synthetic sandwich scaffolding deck
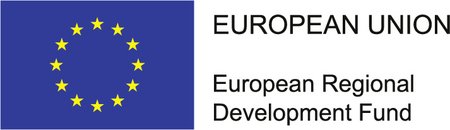
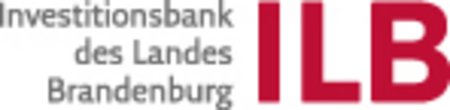
The aim of the project is the development of a novel plastic-based sandwich scaffold covering in ultra-lightweight design as well as an automated process chain for continuous production. The new scaffolding decking must serve as a walking and working surface as well as a place to store building materials or tools. In addition, as a stiffening element, it should contribute to increased stability of the scaffolding. Classical scaffold decking consists of a solid wood plank as well as steel, aluminium and combined materials (e.g. a screen printing plate with an aluminium frame) and often offers a high system weight in addition to high production and material costs. However, current developments in lightweight aluminium profile frames and cover laminates show the growing demand for weight-optimised scaffolding decks and the optimisation potential in this area.
AFP-Prepregs: Development of new prepreg systems for the manufacture of heavy-duty CFRP components
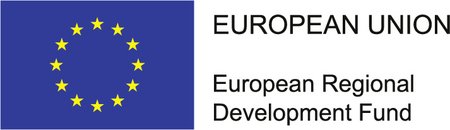
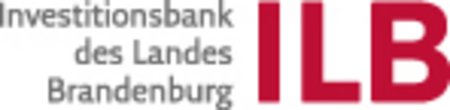
Joint project partners
Fraunhofer Institute for Applied Polymer Research IAP - Prof. Dr. Christian Dreyer,
Chair of Polymer-based Lightweight Design of BTU Cottbus - Senftenberg - Prof. Dr. Holger Seidlitz
Brief description
The aim of the project is the development of tailor-made, processable prepreg resins and semi-finished products for the automated production (Automated Fiber Placement) of extremely high and low temperature stressed fiber composite components (compressor material, cryotank). The project will cover the complete process chain in component development: starting with the development of pure resins, the development and characterization of preprag semi-finished components for preliminary tests, up to pilot production/scaling with the prepreg plant of the Fraunhofer IAP Devision Polymeric Materials and Composites PYCO in Wildau, as well as processing into demonstrators with the AFP plant of BTU and final testing of the components.
Support Framework
Richtlinie des Ministeriums für Wissenschaft, Forschung und Kultur (MWFK) zur Förderung der „Stärkung der technologischen und anwendungsnahen Forschung an Wissenschaftseinrichtungen im Land Brandenburg“ (StaF-Richtlinie)
Project period: 01.01.2020 - 31.12.2021
Flexible autoclave plant for the demand-oriented processing of novel, low-cost and highly resilient prepreg semi-finished products and hybrid fibre-plastic/metal multilayer composites
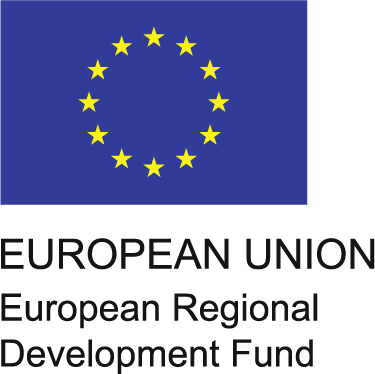
Within the ERDF project "Flexible autoclave plant for the demand-oriented processing of novel, low-cost and highly resilient prepreg semi-finished products and hybrid fibre-plastic/metal multilayer composites", a new autoclave plant was procured for the chair of Polymer-based Lightweight Design. This enables the processing of novel filament-based thermoplastic prepreg systems into temperature-resistant hybrid F-P/M multilayer composites at the university. The autoclave plant completes the processing of thermoset and thermoplastic fibre composite semi-finished products. In combination with low-cost one-piece tools, it will be used for the production of basic demonstrators with complex component geometry and test specimens with high fiber volume content. The hybrid fibre-plastic/metal multilayer composites can be consolidated in the autoclave at a pressure of up to 15 bar and a maximum temperature of 250°C. On 11.02.2020 the plant of the company Italmatic Presse E Stampi srl was delivered to the gates of the laboratory hall 4C on the university campus of BTU Cottbus - Senftenberg in Cottbus. The autoclave system will be assembled and put into operation within the next few weeks.
Energy-efficient composite materials with excellent property profile (EnerVeE)
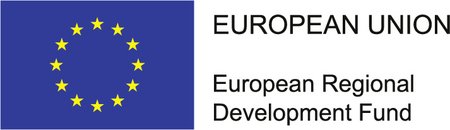
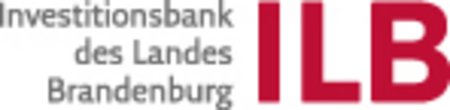
Joint project partners
Fraunhofer Institut für angewandte Polymerforschung - Dr. Dreyer, Prof. Dr. Ganster (Lead-Partner)
Fachgebiet Leichtbau mit strukturierten Werkstoffen der BTU Cottbus - Senftenberg - Prof. Dr. Holger Seidlitz
Forschungsgruppe Polymere Hochleistungsmaterialien der TH Wildau, Prof. Dr. Michael Herzog
Brief description
The aim of the joint project "Energy-efficient composite materials with excellent property profile - EnerVeE" is the development of novel semi-finished fibre composite products and associated system technologies for lightweight construction applications, especially in aircraft and vehicle construction. Representative technology demonstrators are used to identify important engineering principles for material-compatible construction and design as well as for production and processing.
Within the framework of the joint project, the Department of Lightweight Structured Materials deals with the development and validation of a methodology for the reliable coupled process and structure simulation of energy-efficient composite materials with excellent property profiles.
Support Framework
Richtlinie des Ministeriums für Wissenschaft, Forschung und Kultur (MWFK) zur Förderung der „Stärkung der technologischen und anwendungsnahen Forschung an Wissenschaftseinrichtungen im Land Brandenburg“ (StaF-Richtlinie)
Project period: 01.06.2018 - 30.11.2020
German-Polish workshop to strengthen the border region
"German - Polish Innovation Network for sustainable economic/technological strengthening of the border region Spree-Neiße-Bober through need-based qualification and retention of professionals for the region" as part of the Small Projects Fund (KPF) of the Cooperation Program INTERREG V A Brandenburg-Polen 2014-2020. The department of lightweight design with structured materials of Prof. Seidlitz, conduct a joint workshopat the BTU in Cottbus together with Prof. Simon and the Institute for Computer Science and Production Management of the Zielona Góra University of Prof. Kłos. On both days, the students of the respective institutes receive in-depth insights into the current research areas of composites, multi-material design and additive manufacturing in lectures and internships. Within the network, the scientific / technological exchange and the need for action for the coming decades in the field of tension between the hot spots BTU Cottbus - Senftenberg and the University of Zielona Gora with the surrounding companies should be intensified respectively analyzed.
A detailed description of the workshop can be found here in German and in Polish.
Special hot press for the production of new, heavy-duty hybrid fiber-plastic / metal multilayer composites
The aim of the project is to develop new, ultra-light hybrid multilayer composites with improved processing properties. For the first time, thin metal and high temperature resistant thermoplastic fiber composite layers are used.
The new approach represents a cost-effective alternative to the thermoset-based and thus typically brittle hybrid compounds, the manufacture of which is currently associated with long cycle times and a considerable expenditure of raw materials and energy. The technical implementation and further characterization of the new thermoplastic-based material composites require a special hot press, which is the subject of the proposed measure.