Facilities test center
Test benches for components and prototypes
- focus is on hybrid-electric propulsion systems for aircraft
- aligned with the relevant aerospace industry DO160 test specifications
- release-relevant tests can be performed
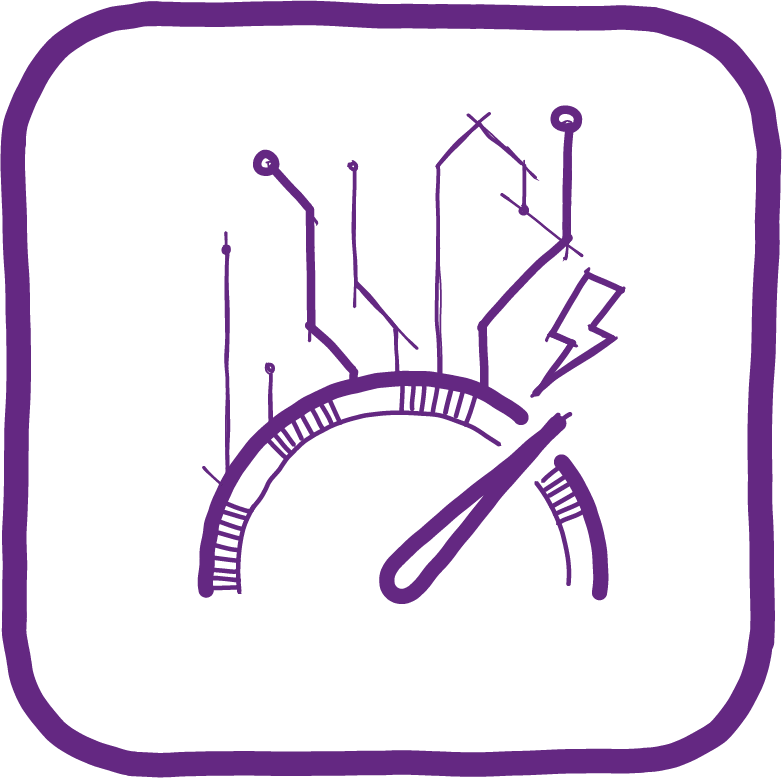
TESI - Test Facility for the Electrical Integrity of the System
- The facility is used to test the entire electro-mechanical drive system
- Test under static and dynamic operation up to full power
- Test under all load and disturbed conditions
- Testing of mutual interferences
- Test on sea level
- Test with failure implementation
- Rated power up to 1.5 MW in single or multi shaft configuration
Future facilities in the new chesco building
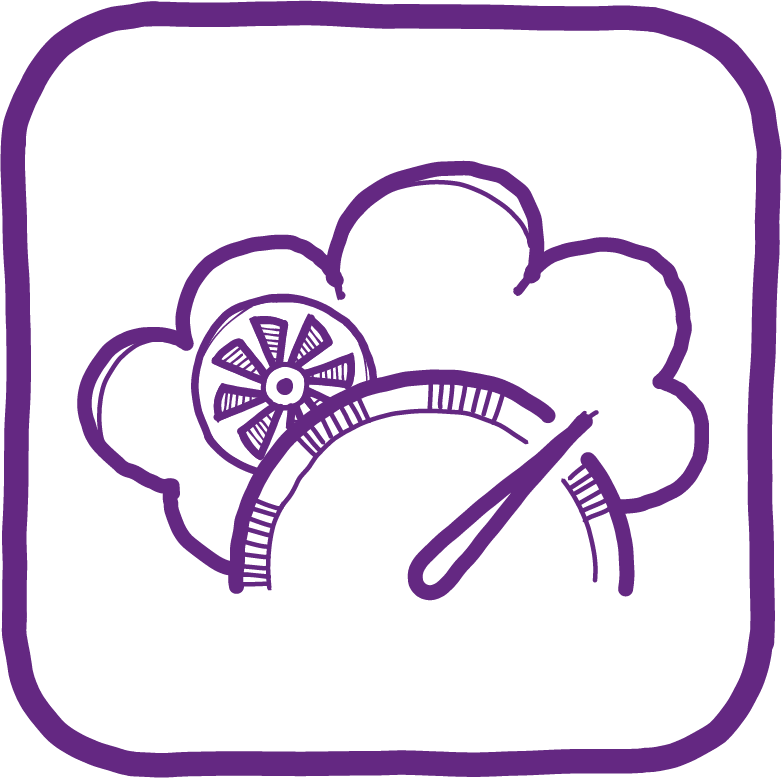
SHP - System High Altitude Test Chamber
- The facility is used to test the static and dynamic operating behavior up to full power
- Test of gas turbines or fuel cells and the entire electrical system
- 250m² electrical test stand (EFT)
- 30m² gas turbine/ fuel cell test stand (GGP)
- Test up to full load conditions of the overall system
- Test on sea level and up to 35 T ft (climatic and pressure chamber)
- Rated power up to 4 MW thermal/ 1.5 MW electric
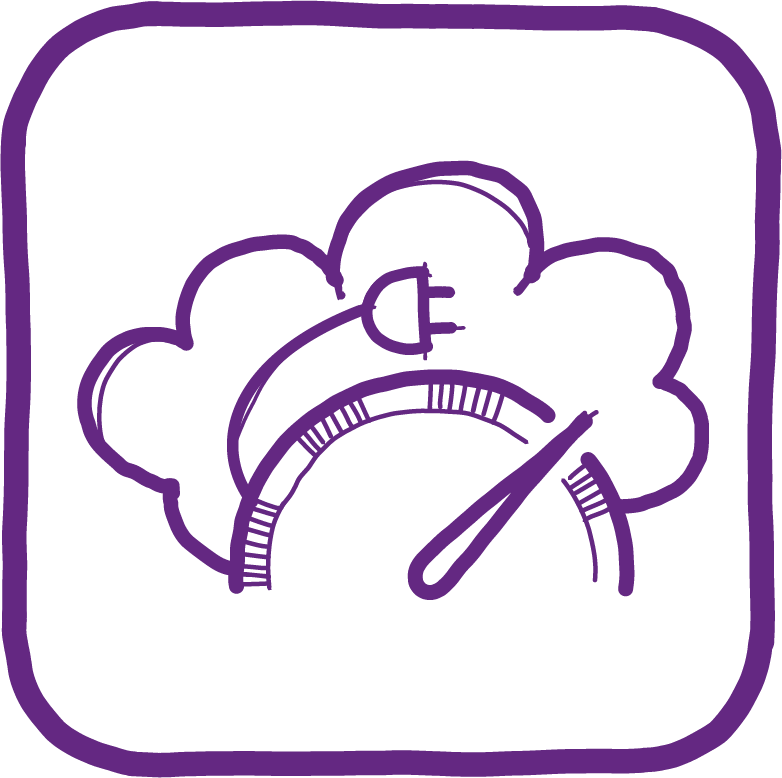
KHP - Small High Altitude Test Chamber
- The facility is used to test individual electrical drive trains or components such as DUT motor and load machine
- Test under static and dynamic operation up to full power
- Test on sea level and up to 35 T ft (climatic and pressure chamber)
- High altitude test chamber: 1,5m x 2,5m x 1m
- Rated power up to 500 kW
- KHP will serve as an altitude chamber for batteries used to power the Devices under test (DUT) in the electrical test filed (ETF)
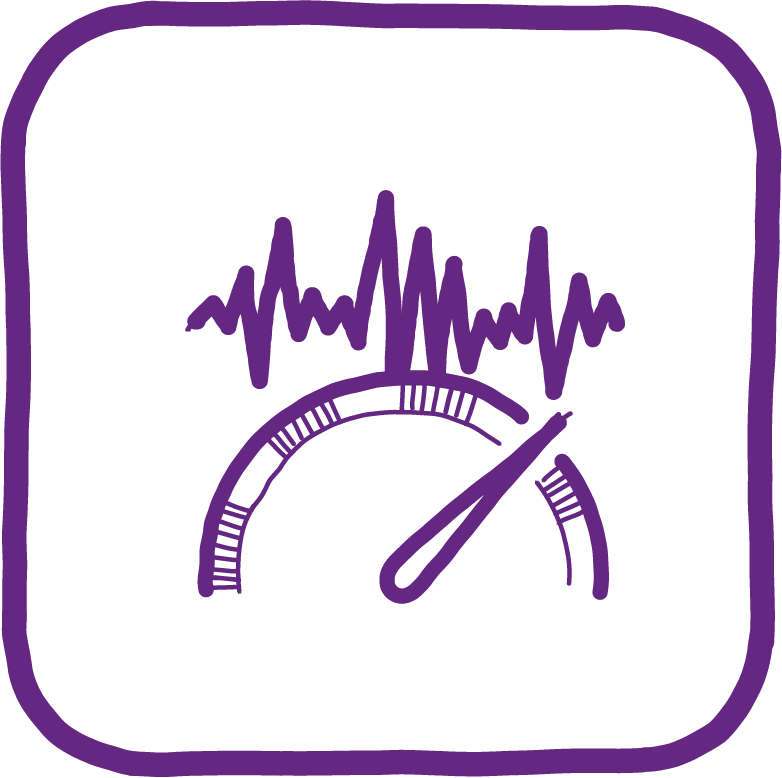
KOVIB - Component Test Bench for Vibration and Shock acc. to DO-160
- The facility is used to test electrical drive trains and components under vibrations and shock
- Test under static and dynamic operation up to full power
- Rated power up to 500 kW
- One direction system
- DUT can be mounted to shake in all three dimensions
- Vibration test bench shaking with 200 kN
- Vibration from 5 Hz up to 2 kHz
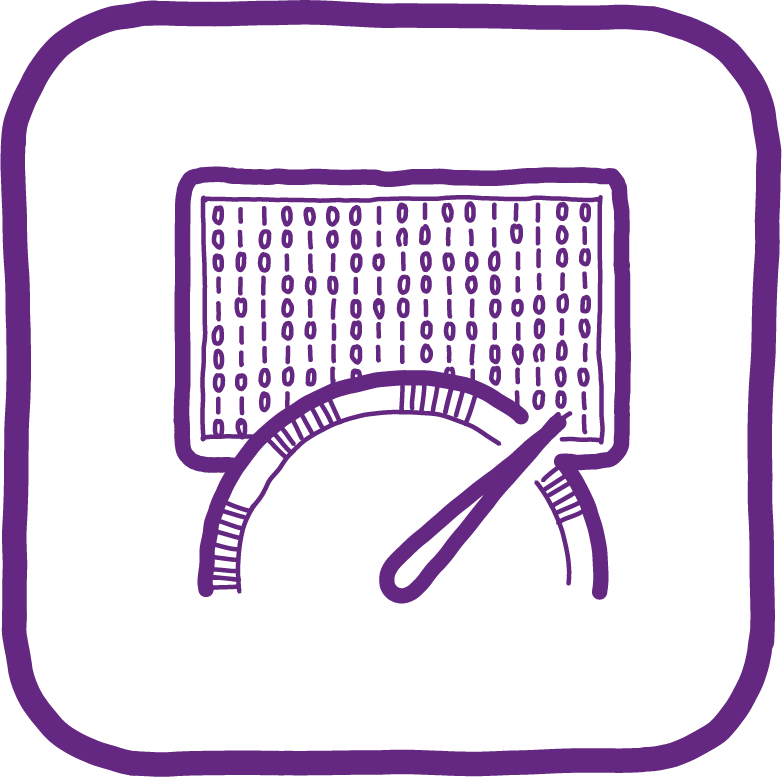
SOFTI - Software Test Facility
- The facility is used to test the entire control hardware and software including cockpit interface (controls copper bird: open and closed loop controls)
- Loading with HiL (Hardware in the Loop) simulators
- Test under load- und overload conditions (at sea level)
- Test with failure implementation
- The entire electrical and electronic systems of an aircraft will be set up in the test room with original cable runs

HOT - High Temperature Test Chamber acc. to DO-160
- The facility is used to verify the remaining operating time of the device under test (DUT) in case of fire in the neighboring area
- Test of non redundant electrical components (e.g., power management or distribution system) under extreme high temperature
- Simulation of operation behind a firewall of the aircraft
- Test under static and dynamic operation up to full power
- The firewall shall be capable of being heated up to 2000°F
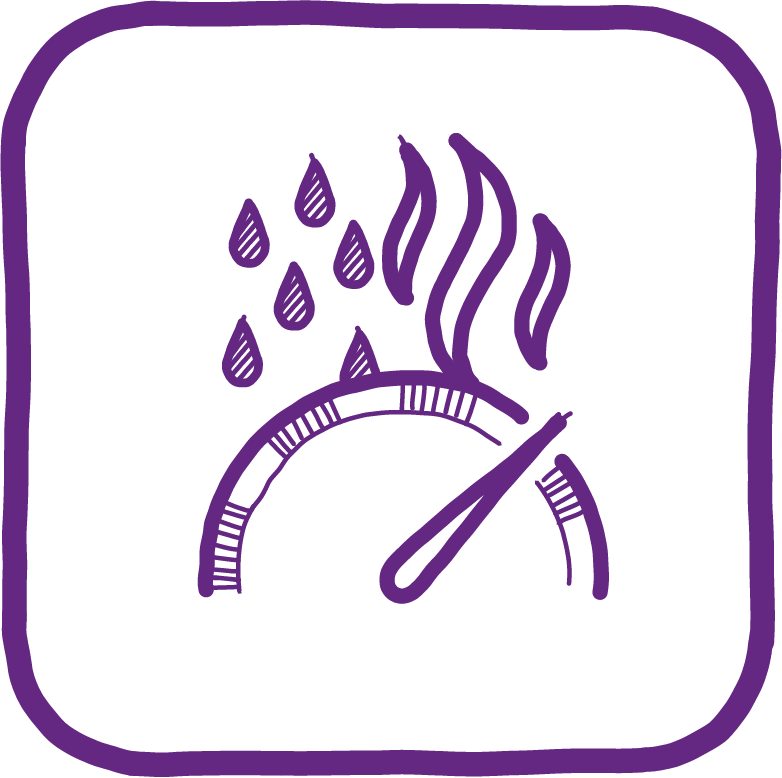
KOKLI - Component Test Bench For Environmelntal Conditions acc. to DO-160
- The facility is used to test the electrical drive trains and components (converters and motors, but not batteries) under extreme environmental conditions such as extreme temperatures, humidity (rain), dust and salt
- Test under static and dynamic operation up to full power
- 4 chambers: climate, sand and dust, salt, rain
- Rated power up to 500 kW

COOL - Test Bench for Heat Exchangers and Cooling Devices
- The facility is used to test the heat exchangers and cooling units
- Test under static and dynamic operation up to full power
- Test of complete cooling devices up to 400 kW
- Cyclic testing
- Mechanical loads can be applied
- Test from -55°C up to +150°C
Establishment of a test center network with the DLR Institute of Electrified Aero Engines
Brandenburg is developing into an important aviation region in Germany. Major international corporations, local enterprises, universities, and the German Aerospace Center (DLR) are researching, developing and producing low-emission aviation in our region. In this context, comprehensive testing facilities are a prerequisite for verifying the results of research and development towards zero emission aviation and certifying them on their way to application and market readiness. With the Center for Hybrid Electric Systems Cottbus (chesco) of the Brandenburg University of Technology Cottbus Senftenberg (BTU) and the Hybrid Electric Propulsion Cottbus- Test Facilities (HepCo) of the DLR Institute of Electrified Aero Engines, a network of centers is being established in Cottbus.
The facilities pursue a holistic approach by building on each other in their areas of responsibility and focusing on both component and system testing. The respective testing capacities are closely coordinated and aligned, so that the testing options complement each other. High-precision and technologically complex test and inspection facilities, including large-scale facilities, are being created to cover all areas of safety-relevant testing for basic research and product development for low- and zero-emission aircraft engines across a wide range of technologies and Technology Readiness Levels (TRL). Furthermore, the verification and validation activities required for product approval, especially on component and (sub-) system level, will be enabled.
The range of these components and (sub-)systems extends from aircraft sizes for general aviation to commercial aviation with up to 70 passengers and, depending on technical feasibility, even beyond in the long term.
The joint test bench landscape is being established on the grounds of the Lausitz Science Park near the main campus of the BTU.