Das nasschemische Ätzen von Silicium mit Flusssäure-Salpetersäure-Gemischen
Das nasschemische Ätzen mit Flusssäure-Salpetersäure-Gemischen (HF/HNO3-Gemischen) ist einer der essentiellen Prozessschritte in der Fertigung von Solarzellen aus multikristallinem Silicium sowie in der Mikroelektronik.
Seit den ersten systematischen Untersuchungen wird das isotrope, nasschemische Ätzen von Silicium mit HF/HNO3-Mischungen in der Literatur mit der folgenden Bruttoreaktionsgleichung beschrieben [1-4]:

Dieser Reaktionsgleichung liegt die formale Annahme zugrunde, dass die Salpetersäure Silicium entsprechend Gl. (2) zu SiO2 oxidiert wird und dabei selbst zu NO reduziert wird.

Das gebildete Oxid wird anschließend von Flusssäure unter Bildung von SiF4 nach Gl. (3) gelöst.

In Gegenwart von weiterer HF wird das entstandene SiF4 nahezu vollständig in den wasserlöslichen Komplex SiF62- überführt (Gl. (4)).

Zahlreiche Untersuchungen der vergangenen Jahre haben gezeigt, dass dieses einfache Modell des Ätzens weitgehend unzutreffend ist. Dies belegen beispielhaft die folgenden Fakten:
- Durch XPS-Untersuchen konnte die Existenz einer SiOx-Schicht widerlegt werden [5],
- es wurden N2O [6,7] und NO2 [7] als gasförmige Reaktionsprodukte des Ätzens bei Raumtemperatur nachgewiesen,
- unterhalb von Raumtemperatur gelang der spektroskopische Nachweis von gelöstem N2O3, gelöstem N2O2 und NO+ als Intermediate des Ätzens [8],
- die intermediären Stickstoffspezies in der Oxidationsstufe +3 werden beim Verdünnen in Nitritionen umgewandelt, die sich analytisch leicht bestimmen lassen [9],
- NO+, wurde als reaktives Spezies im geschwindigkeitsbestimmenden Schritt des Ätzens in konzentrierten Säuregemischen nachgewiesen [8],
- Salpetersäure wird während des Ätzens teilweise bis zum Ammonium-Ion reduziert [10],
- Wasserstoff wurde als ein Produkt des Ätzens nachgewiesen, der besonders in HF-reichen Ätzmischungen in beträchtlichen Mengen gebildet wird [6,11].
Obwohl mittlerweise ein prinzipielles Verständnis der Reaktionsschritte am Silicium besteht, sind viele Details des Reaktionsmechanismus noch immer unbekannt.
Ein Ziel unserer Forschungen ist die weitere Aufklärung des Ätzmechanismus, dessen kinetische Beschreibung sowie die Identifizierung und Quantifizierung der Reaktionsprodukte und Intermediate, die während des Ätzens in den HF/HNO3-Lösungen entstehen.
Auch der industrielle Ätzprozess in der Solarzellenfertigung ist Gegenstand unserer Forschungsarbeiten. Hier beschäftigen wir uns u.a. mit Fragen der Texturierung von Solarzellen (Oberflächenstrukturierung), dem ressourcenschonenden Einsatz der Ätzchemikalien sowie der Prozessanalytik und Prozesssteuerung.
Das Auflösen von Silicium in konzentrieren HF/HNO3 Ätzlösung bei Raumtemperatur führt zu einer heftigen Entwicklung von braunen Stickoxidgasen (Abb. 1). Als einziges gasförmiges Reaktionsprodukt gemäß Gl. 1 sollte NO entstehen, welches mit Luftsauerstoff bei Raumtemperatur zu braunem NO2 oxidiert wird. Doch entweichen die beim Ätzen entstandenen Gase nicht vollständig aus der Ätzlösung. Die gute Löslichkeit von NO2 in Salpetersäure führt zur Gelb- bzw. Braunfärbung der Ätzlösung.
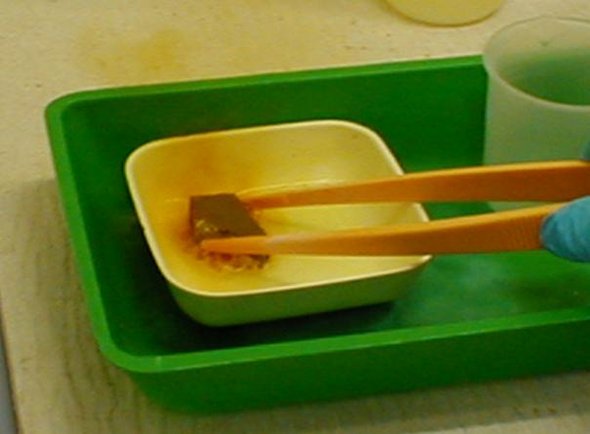
Wird der Auflöseprozess bei Temperaturen unter 15 °C durchgeführt, verfärbt sich die Ätzmischung zunächst nach grün und nimmt bei 1 °C eine himmelblaue Farbe an (Abb. 2). Im Vergleich zu Experimenten bei Raumtemperatur nimmt die Bildung des braunen Gases bis auf Spuren ab.
Abbildung 3 gibt einen Überblick über die im Rahmen unserer Forschungsaktivitäten und durch andere Gruppen gefundenen Stickstoffintermediate und die von uns vermuteten Reduktionswege der Salpetersäure. Alle in rot aufgeführten Spezies wurden durch verschiedene analytische Methoden nachgewiesen. Die Spezies in schwarzer Schrift stellen vermutete Intermediate oder Endprodukte dar, deren experimenteller Nachweis noch nicht gelungen ist.
In einem ersten Zweielektronenschritt erfolgt die Reduktion von HNO3 (N(V)) zu N(III)-Intermediaten wie N2O3, und [N4O62+], die untereinander im Gleichgewicht stehen. Das gelöste Distickstofftrioxid bewirkt die intensive Blauverfärbung der Ätzlösung. N2O3 zerfällt entweder in die Bestandteile NO und NO2 oder wird durch Luftsauerstoff oxidativ zu HNO3 abgebaut. Beim Verdünnen einer konzentrierten Ätzmischung wandeln sich alle vorliegenden N(III)-Intermediate vollständig in Nitritionen um, deren Gehalt mittels Ionenchromatographie bestimmt werden kann. Dies unterstreicht die Wichtigkeit der Nitritkonzentration als nützlichen Summenparameter zur Beschreibung der Reaktivität von Ätzmischungen in industriellen Anwendungen.
Die weitere Reduktion der in Lösung vorliegenden Spezies führt letztlich zur Bildung von Ammonium-Ionen. Damit ist zu vermuten, dass ein Teil der Intermediate sukzessive in drei aufeinanderfolgenden Zweielektronenschritten bis zur Oxidationsstufe -3 (NH4+) reduziert werden.
Multikristallines Silicium wird in rechteckigen Blöcken von mehreren 100 kg kristallisiert, indem die Erstarrungsfront vom Boden des Gefäßes langsam zur Oberseite wandert. Nach dem Entfernen aller Randflächen, die mit dem Tiegelmaterial in Berührung gekommen sind, sowie der Oberseite, werden die Blöcke zunächst in quadratische Säulen zerteilt, aus denen in einem nachfolgenden Prozessschritt die Wafer (as cut wafer) gesägt werden. Die Oberflächen der as cut Wafer weisen eine stark gestörte Kristallstruktur auf, den sogenannten Sägeschaden (Abb. 4), der entfernt werden muss, da aufgrund dieser enormen Kristallstörungen die bei der Absorption des Sonnenlichtes entstehenden Elektron-Loch-Paare so schnell miteinander rekombinieren, dass eine daraus hergestellte Solarzelle praktisch keinen Strom liefern kann.
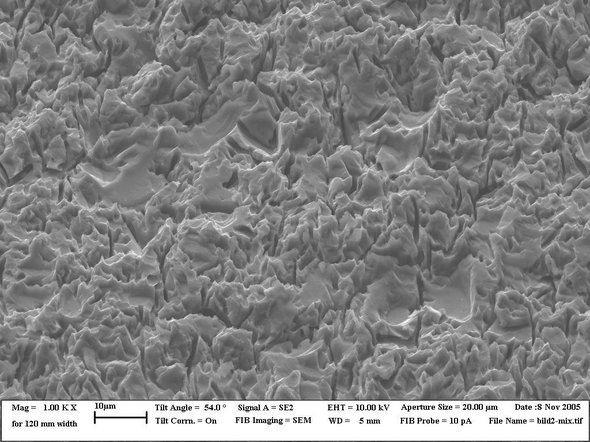
Zur Entfernung dieser gestörten Kristalloberfläche von multikristallinen Wafern werden ausschließlich saure Ätzgemische eingesetzt, die Flusssäure, Salpetersäure, Wasser sowie weitere Zusätze, wie Schwefelsäure oder Tenside enthalten können. Durch das gezielte Abätzen des Sägeschadens wird zunächst die Voraussetzung für eine funktionsfähige Solarzelle geschaffen, indem die photophysikalisch inaktive Schicht entfernt wird. Zusätzlich wird der Waferoberfläche eine gewisse räumliche Struktur aufgeprägt, die sogenannte Textur, welche von entscheidender Bedeutung für die effektive Nutzung des einfallenden Sonnenlichtes ist. Angestrebt wird eine hohlspiegel- oder pyramidenartige Texturierung (Abb. 5), welche die von der Waferoberfläche reflektierten Lichtstrahlen des Sonnenlichtes nicht unmittelbar in den Raum zurück wirft, sondern auf andere Stellen der Oberflächenstruktur lenkt (Mehrfachreflexion). Dort kommt es zu erneuten Absorption des Sonnenlichtes, die zu einer höheren Lichtausbeute führt und damit den Wirkungsgrad der Solarzelle steigert. Die Messgröße "Reflektivität" beschreibt diesen Umstand; je geringer ihr Wert ausfällt, umso mehr Licht wird innerhalb der Oberfläche reflektiert.
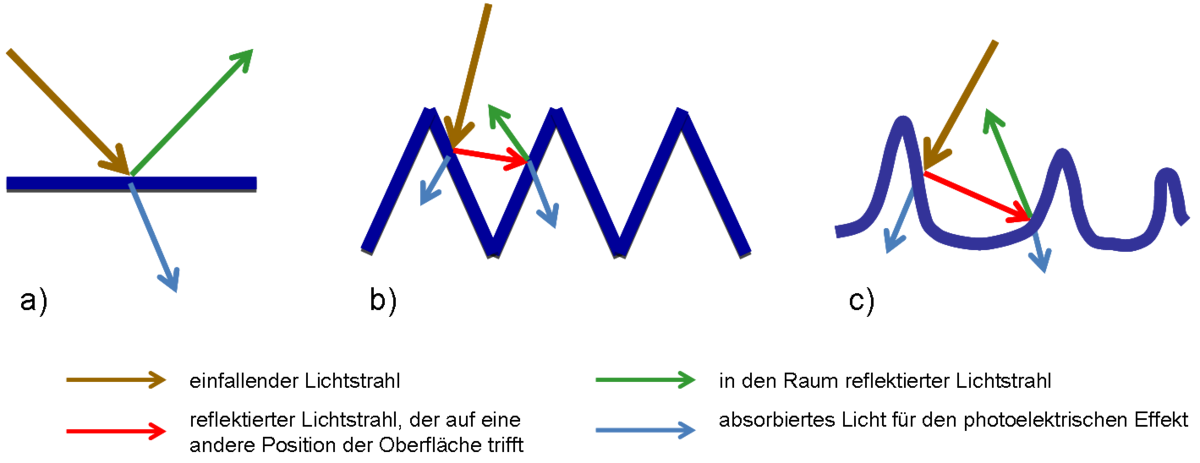
Die erforderliche Oberflächenstruktur entsteht nur, wenn nach der Entfernung des Sägeschadens auch die darunterliegende ungestörte Kristallstruktur in geringem Ausmaß abgetragen wird. Eine zu lange Ätzdauer führt zur Einebnung der Textur und zur Entstehung sehr ebener, spiegelnder Oberflächen ohne Mehrfachreflexion, woraus eine mit Solarzelle geringerem Wirkungsgrad resultieren würde.
Für das Texturieren von Solarwafern kommen in der Regel salpetersäurereiche Mischungen mit einem Anteil von Wasser zum Einsatz (Abb. 6). Daraus resultiert eine geringere Ätzrate als für konzentrierte Säuregemische, doch kann der zu erzielende Abtrag recht genau eingestellt werden. Die ablaufenden Prozesse beim Texturieren sind bislang noch nicht vollständig bekannt, da sich sowohl das reaktiven Spezies, die Ätzkinetik, die Art und Konzentration der entstehenden Intermediate wie auch die Stöchiometrie der Reaktion (d.h. der Umsatz der vorgelegten Säuren) erheblich von den Vorgängen in konzentrierten Säuregemischen unterscheiden.
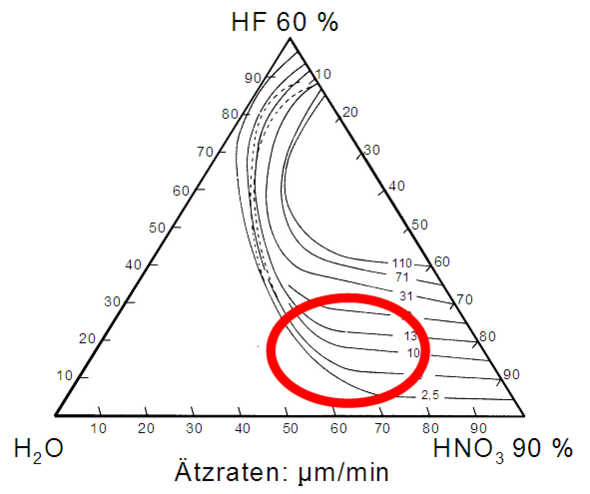
Am Beispiel von zwei Ätzversuchen mit Gemischen aus Salpetersäure und Flusssäure sollen die komplexen Abhängigkeiten zwischen den eingesetzten Säuremischungen und der resultierenden Reflektivität der damit geätzten Wafer verdeutlicht werden.
Wie die rasterelektronenmikroskopische Aufnahme in Abb. 7a zeigt, besitzt die Oberfläche eines as cut Wafers eine rauhe, sägezahnartige Struktur, die über eine Vielzahl glatter und über mehrere Mikrometer ausgedehnte Bruchflächen aufweist. Daraus resultiert ein vergleichsweise hoher Reflektionsgrad von R=26 %, der als Anfangswert für die folgenden Untersuchungen dient.
Ein kurzzeitiges Ätzen bewirkt bereits eine deutliche Veränderung der Oberflächenstruktur. Abb. 7b zeigt, dass die für den Sägeprozess typische Struktur der ausgedehnten Bruchflächen bereits nach 10s Ätzen teilweise verschwindet und schmale, tiefe Gräben freigelegt werden, die in den rasterelektronenmikroskopischen Aufnahmen als schwarze Linien erscheinen. Diese Gräben, die sowohl senkrecht als auch schräg im Silicium verlaufen können, entstehen durch die Krafteinwirkung während des Sägens. Mit zunehmender Ätzdauer (Abb. 7c) nimmt der Anteil an tiefen schmalen Gräben ab, während sich die noch verbleibenden Gräben immer mehr verbreitern. Zudem bilden sich die ersten größeren ovalen Ätzgruben heraus. Nach einer Ätzdauer von ca. 90s ist die typische Textur entstanden (Abb. 7d).
Diese Strukturentwicklung spiegelt sich auch im Verlauf des Reflektionsgrades über den Dickenabtrag in Abb. 8 wider. Der Reflektionsgrad sinkt ausgehend vom as cut wafer mit 26 % zunächst stark ab, weil sich die reflektierende Oberfläche durch die freigelegten Gräben erheblich verringert hat. Der zunehmende Abtrag bewirkt ein generelles Verbreitern der Strukturen und gleichzeitig ein zunehmendes Verflachen der ursprünglich tiefen Gräben, weshalb der Reflektionsgrad sukzessive wieder ansteigt.
Der Verlauf des Reflektionsgrades über den Abtrag kann in Abhängigkeit von der eingesetzten Ätzmischung wie auch von den gewählten Ätzbedingungen mehr oder weniger deutlich variieren. Abb. 8 zeigt beispielsweise, wie für Ätzmischungen (ÄM) mit steigendem HF-Gehalt bei konstantem HNO3-Gehalt der Reflektionsgrad mit zunehmendem Abtrag nahezu einheitlich ansteigt. Alle erzielten R-Werte liegen niedriger als für den unbehandelten Wafer.
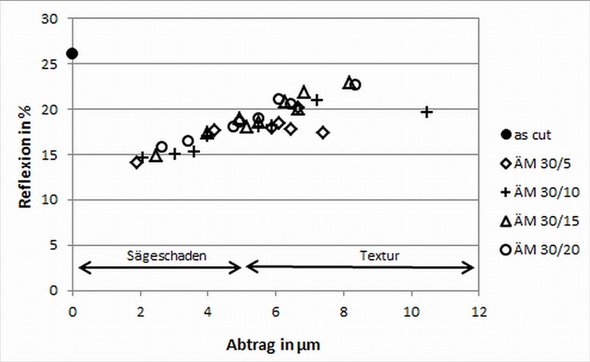
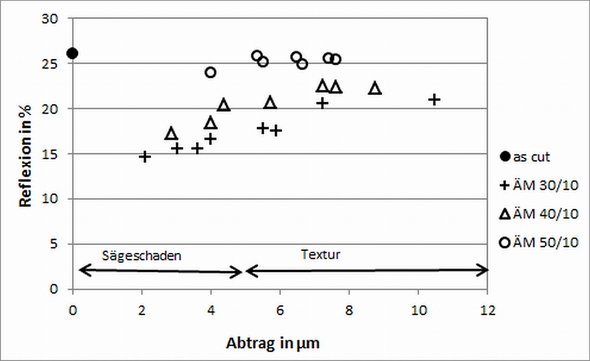
Werden dagegen bei einem konstanten Gehalt von 10 % (m/m) Flusssäure die Anteile an HNO3 im Bereich von 30 % (m/m) bis 50 % (m/m) variiert, ist eine deutliche Abhängigkeit des Reflektionsgrades vom Abtrag zu erkennen (Abb. 9). Die Reflexionswerte steigen mit zunehmendem HNO3-Gehalt an. Somit können nach der vollständigen Entfernung des Sägeschadens im Bereich der Texturierung Reflektionsgrade von 20 % und weniger erreicht werden.
Das Ätzen des Sägeschadens wird maßgeblich durch die Struktur der gestörten Oberfläche bestimmt. Die verschiedenen Verfahren der Kristallisation (Czochralski-Verfahren, Blockerstarrung, cast-mono-Silicium) und der Sägetechnologien (slurry-Trennprozess, Diamant-Drahtsägeprozess) führen zu unterschiedlichen Strukturen nach dem Trennen, die zu jeweils unterschiedlichen Anforderungen beim Ätzen führen.
Eine aktuelle Herausforderung ergibt sich durch das Sägeverfahren. Für das Sägen der Bricks zu Wafern kommen gegenwärtig zwei verschiedene Verfahren zum Einsatz, die sich technologisch wie auch in der Struktur des Sägeschadens unterscheiden.
Beim Drahtsägeverfahren wird ein ca. 110-140 µm dünner Stahldraht bei einer Geschwindigkeit von ca. 10-20 m/s gemeinsam mit einen Glykol-Siliciumcarbid-Gemisch (slurry) als Schleifmittel über den Block geführt. Der für die Trennung erforderliche Materialabtrag erfolgt durch die Siliciumcarbidkörner, die lokale Deformationen und Brüche und damit letztlich das Abplatzen von Siliciumpartikeln hervorrufen.
Die hohe Abnutzung des Sägedrahtes, des Schleifmittels und die komplexe Aufbereitung der gebrauchten Slurry, speziell des darin enthaltenen Siliciumcarbides, haben in den letzten Jahren zur Entwicklung des Diamantdraht-Sägeverfahrens geführt. Hierbei erfolgt die Trennung durch einen mit kleinen Diamantkristallen besetzten Stahldraht, ohne dass zusätzlich ein Schleifmittel notwendig ist. Die Sägezeiten verkürzen sich um die Hälfte und führen zu einer deutlichen Produktivitätssteigerung.
Am Beispiel für zwei unterschiedlich gesägte Wafer und dem daraus resultierenden Sägeschaden wird die Reflektivität der Oberflächen verdeutlicht.
Wie die rasterelektronenmikroskopische Aufnahmen in Abb. 9 (a und b) zeigen, besitzt die Oberfläche eines slurrygesägten as cut Wafers eine gleichmäßig matte und raue, sägezahnartige Struktur, die eine Vielzahl ausgedehnter Bruchflächen aufweist. Daraus resultiert ein Reflexionswert von R=24 %. Die Oberfläche eines diamantdrahtgesägten Wafers schimmert dagegen silbrig und bereits mit bloßem Auge lassen sich Rillen und streifenförmige Strukturen erkennen. Mit R=26 % besitzt der diamantdrahtgesägte Wafer eine deutlich höhere Reflexion. Die rasterelektronenmikroskopischen Aufnahmen in Abb. 9 (c und d) lassen zwei unterschiedliche Merkmale erkennen: Es existieren sowohl glatte wie auch raue Bereiche mit Rissen und Bruchflächen.

Diese Strukturen können das das Messergebnis erheblich beeinflussen. Zur Bestimmung der Reflexion wird eine Ulbricht-Kugel verwendet, bei der der Messstrahl nicht senkrecht auf die Probe trifft. Damit wird die gemessene Reflexion zusätzlich durch die Ausrichtung der Rillen und Streifen der diamantdrahtgesägten Wafer gegenüber der Richtung des einfallenden Lichtstrahls bestimmt, so wie in Abb. 11 schematisch dargestellt. Für slurrygesägte Wafer mit ihrer einheitlicheren Oberflächenstruktur hat die Ausrichtung keinen Einfluss auf das Messergebnis.
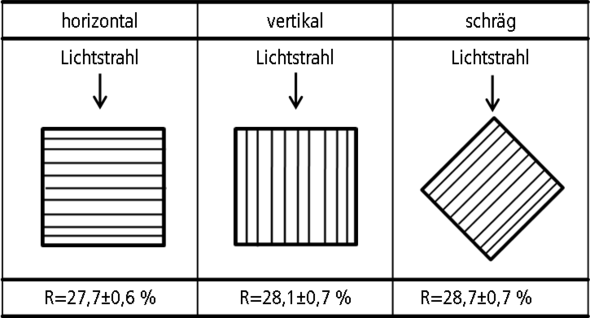
Slurrygesägte und diamantdrahtgesägte Wafer offenbaren auch beim sauren Ätzen ein etwas unterschiedliches Verhalten. Wie Abb. 12 für einen slurrygesägten Wafer zeigt, führt bereits ein geringer Ätzabtrag im Bereich des Sägeschadens (< 4 µm) zur Abnahme der Reflexion. Vermutlich liegt dies in der sukzessiven Entfernung der sägezahnartigen Strukturen (Abb. 4 und 10a) begründet, die wie Mikrospiegel die hohe Reflexion der gesägten Wafer verursachen. Mit zunehmendem Abtrag und der sich ausbildenden Textur steigen die R-Werte stetig an, ohne den hohen Anfangswert zu erreichen. Nach 8 µm Abtrag wird eine typische Textur mit zahlreichen großen und kleinen Mulden beobachtet (Abb. 13)
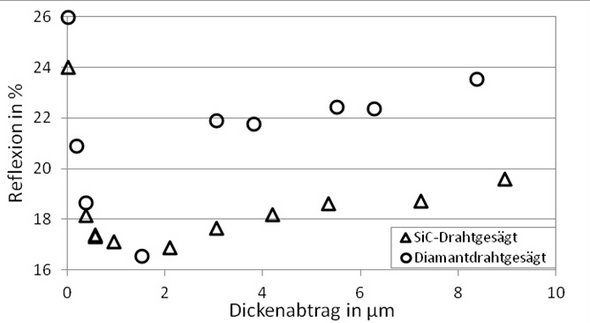
Diamantdrahtgesägte Wafer zeigen, wie aus Abb. 12 ersichtlich, einen ähnlichen Verlauf. Die Reflektivität sinkt noch im Gebiet des Sägeschadens deutlich ab und steigt dann mit zunehmendem Abtrag wieder an, allerdings deutlich über die Werte der slurrygesägten Wafer. Wie in Abb. 13 zu erkennen ist, erfolgt der Ätzangriff bevorzugt an den durch das Sägen entstandenen Rissen und Bruchflächen, welche bald die typische, muldenartige Textur aufweisen. Die glatten Bereiche der Oberflächenrillen bleiben zunächst weitgehend unverändert. Erst nach vergleichsweise langen Ätzzeiten gelingt die vollständige Texturierung der Waferoberfläche. Damit wird deutlich, dass bisherige Ätzverfahren nicht auf diamantdrahtgesägte Wafer übertragbar sind. Aus der Einführung des neuen und effizienteren Diamantdraht-Sägeverfahren wird es notwendig, das nasschemische Ätzen dahingehend zu optimieren, dass für nicht zu lange Ätzzeiten eine ganzflächig homogene Textur mit mindestens ebenso niedrigen Reflexionswerten erzielt wird, wie dies gegenwärtig für die texturierten, slurrygesägten Wafer erzielt wird.
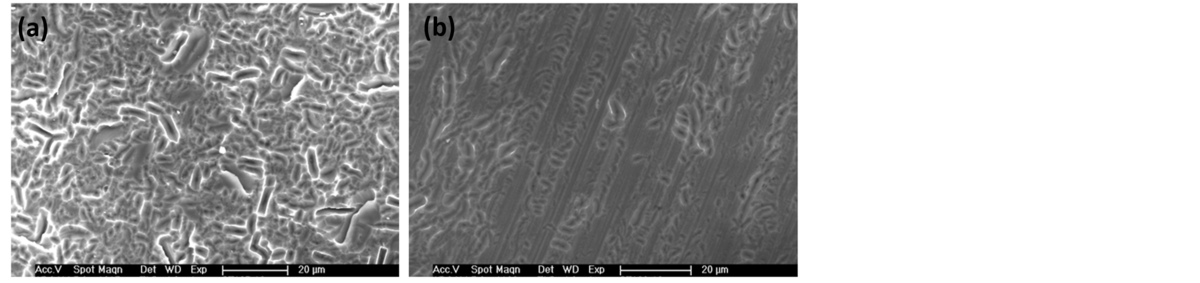
Literatur
(1) | Robbins, H.; Schwartz, B. "Chemical Etching of Silicon." J. Electrochem. Soc. 1959, 106 (6), 505-508. |
(2) | Robbins, H.; Schwartz, B. "Chemical Etching of Silicon." J. Electrochem. Soc. 1960, 107 (2), 108-111. |
(3) | Schwartz, B.; Robbins, H. "Chemical Etching of Silicon." J. Electrochem. Soc. 1961, 108 (4), 365-372. |
(4) | Schwartz, B.; Robbins, H. "Chemical Etching of Silicon." J. Electrochem. Soc. 1970, 123 (12), 1903-1909. |
(5) | Steinert, M.; Acker, J.; Oswald, S.; Wetzig, K. "Study on the Mechanism of Silicon Etching in HNO3-rich HF/HNO3 Mixtures." J. Phys. Chem. C 2007, 111 (5), 2133-2140. |
(6) | Kooij, E. S.; Butter, K.; Kelly, J. J. "Silicon Etching in HNO3/HF Solution: Charge Balance for the Oxidations Reaction." Electrochem. Solid State 1999, 2 (4), 178-180. |
(7) | Weinreich, W. "Grundlegende Schritte des nasschemischen Ätzprozesses von Si-Wafern: Bilanzierung und Steuerung." Diploma Thesis, Technische Universität Bergakademie Freiberg, Germany, 2005 |
(8) | Steinert, M.; Acker, J.; Krause, M.; Oswald, S.; Wetzig, K. "Reactive species generated during wet chemical etching of silicon in HF/HNO3 mixtures." J. Phys. Chem. B 2006, 110 (23), 11377-11382. |
(9) | Steinert, M.; Acker, J.; Henssge, A.; Wetzig, K. "Experimental studies on the mechanism of wet chemical etching of silicon in HF/HNO3 mixtures." J. Electrochem. Soc. 2005, 152 (12), C843-C850. |
(10) | Steinert, M.; Acker, J.; Wetzig, K. "New aspects on the reduction of nitric acid during wet chemical etching of silicon in concentrated HF/HNO3 mixtures." J. Phys. Chem. C 2008, 112, 14139-14144. |
(11) | Hoffmann, V.; Steinert, M.; Acker, J. "Analysis of gaseous reaction products of wet chemical silicon etching by conventional direct current glow discharge optical emission spectrometry (DC-GD-OES)." J. Anal. At. Spectrom. 2011, 26, 1990-1996. |