Areas of application
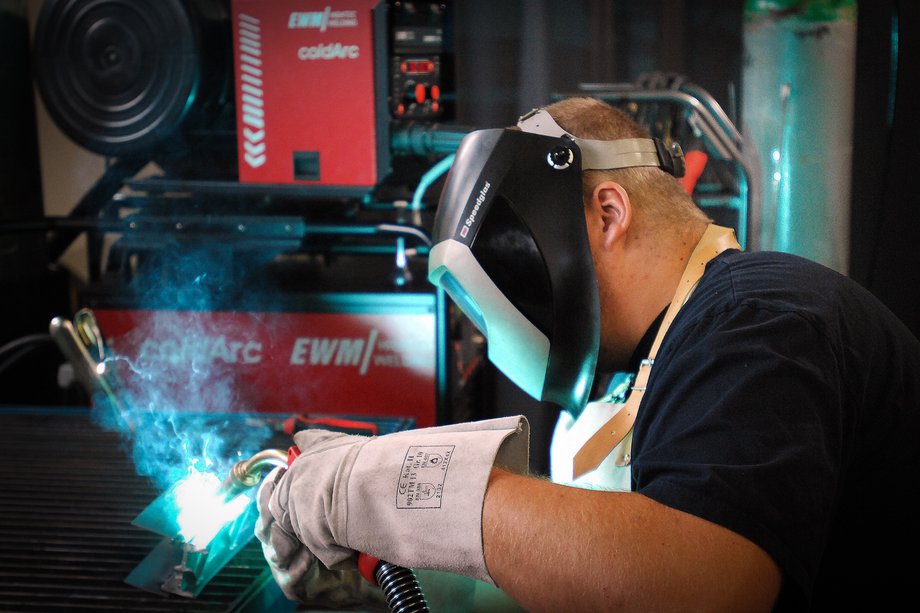
- Welding of thin sheets up to 0.3 mm
- Joining of dissimilar joints, e.g. steel-Al
- Low distortion welding due to minimal heat input
- Build-up welding with low mixing between filler and base material
- Flux-cored welding
- Optimisation of seam quality through targeted alloying
- Determination of optimal process design and control for joining
- Data analysis and process control
- Joining of ceramics
Procedure
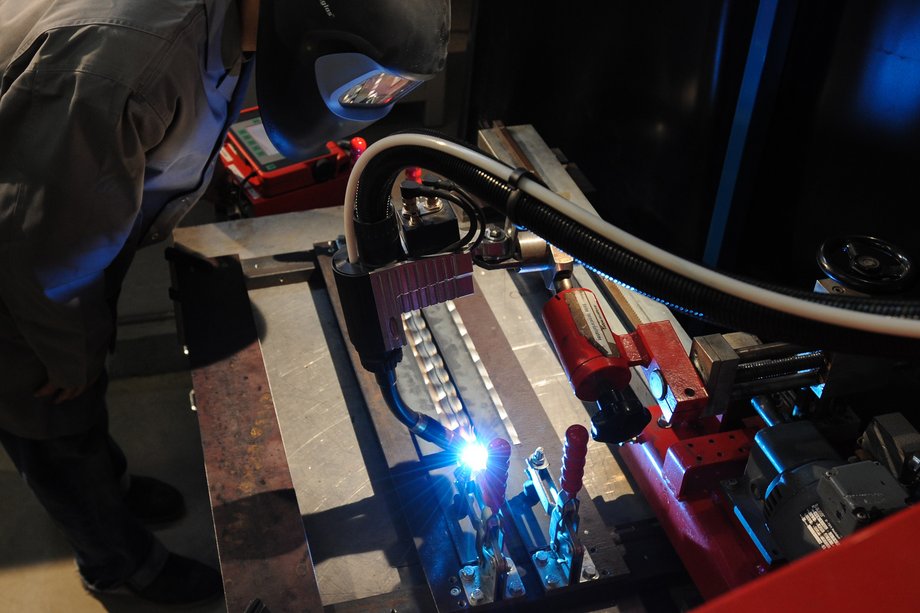
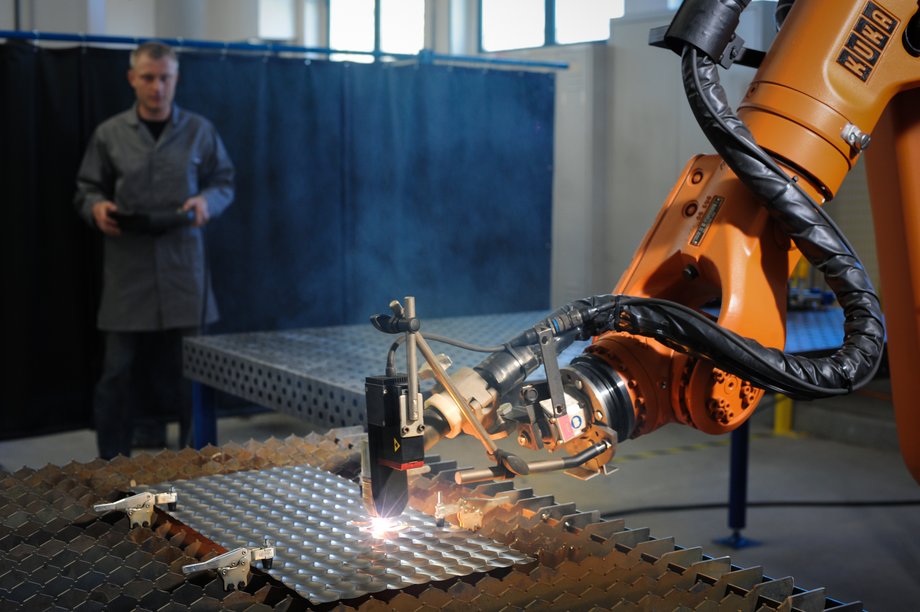
- E-hand welding
- MIG/MAG standard/pulse welding*
- TIG standard/pulse welding*
- Plasma beam welding with non-transmitting arc
- MIG brazing*
- Cold-Metal-Transfer® (CMT) welding*
- ColdArc® welding*
- Submerged arc welding
- Plasma deposition welding
- Pulse friction stir welding
- Resistance spot welding
- Mechanical joining
- Conventional laser beam welding (with and without filler metal)
- Remote laser beam welding
- Laser hybrid process
- Laser cutting
- Plasma cutting
* We also carry out these processes fully automatically.
More information on selected procedures
Cold Metal Transfer® (CMT)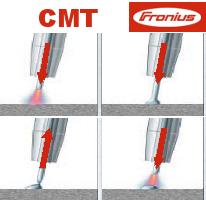
Cold Metal Transfer® process
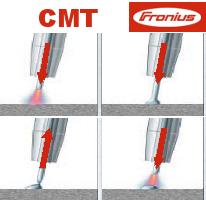
Application areas
- Splash-free welding and brazing
- Thin sheet metal applications
- Thick-thin sheet connections
- Arc joining of dissimilar materials:Steel - SteelAl - AlMg - MgSteel - AlAl - MgSteel - Mg (under investigation)
Process
- Arc welding process with new method for droplet detachment
- Back and forth movement (70 times per second) of the wire
- Droplet transfer with lower heat input compared to conventional arc processes
Advantages
- Low distortion
- High gap bridgeability
- High efficiency due to high welding speeds
- Good automation and all known MSG advantages
Cold Arc welding
Application areas
- Splash-free welding
- Thin sheet applications
- Reduced energy input
- Mixed joints
- Materials:Steel - SteelAl - AlMg - MgAl - Galvanized steelAl - MgMg - Galvanized steel
Process
- Arc welding process with new method for droplet detachment
- Droplet transfer with lower heat input compared to conventional arc processes
Advantages
- Lowest material distortion
- Seam geometry can be individually influenced
- Excellent gap bridgeability
- High efficiency due to high welding speeds
- Insensitivity to environmental influences
- Good automation and all known MSG advantages
Submerged arc welding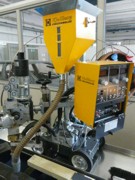
Submerged arc welding system
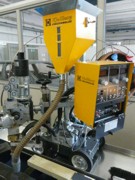
Areas of application
- Steel construction, tank construction, shipbuilding
- Inlay welding up to 25 mm wall thickness
- materials:
- unalloyed, low-alloyed, high-alloyed steels
- Nickel-based alloys
Process
- High deposition rate - up to 15 kg/h
- Variation of welding parameters
- Current: 300-1200 A
- Voltage: 25-40 V
Advantages
- High thermal efficiency - up to 70%
- Selective influenceability of the seam formation
- High gap bridgeability, multi-layer welds
- High efficiency due to high welding speeds
- Insensitivity to environmental influences
- Good automation capability
Resistance spot welding
Areas of application
- Automotive and rail vehicle construction, container construction, equipment and cabinet construction, electrical industry.
- materials:
- unalloyed, low-alloyed, high-alloyed steels, coated steel sheets
- aluminium alloys etc.
Advantages
- good automation
- short process times under 1 s
- joints of different sheet thicknesses and material combinations
- multi-sheet welding
- little or no rework
- high economic efficiency due to short process time typical for this method
Equipment
- Resistance spot welding gun with medium frequency technology, Düring type X 100 ALU
- stationary resistance spot welding machine in console design with alternating current technology Fa. EST Type TPSBM 2132
- SPATZ Multi04 weld data recorder with measuring channels for current, voltage, force (current measuring range 3 steps: 2 kA, 20 kA and 200 kA) and integrated quality documentation
- Electrode cutter
Materials
- Fine-grained steels
- High alloy steels
- Cast steel and cast iron
- Aluminium
- Aluminium die casting
- Magnesium
- Titanium
- Nickel-based alloys
- Copper
- Technical ceramics
- Foreign compounds
Offline programming system SKM DCAM for laser beam processing and robotics
- 2D/3D CAD function
- Tool simulation
- Plant simulation up to 6 axes - module package cutting 5 axes
- CAM modules laser powder and laser wire build-up welding
- Support for Trumpf offline programming
- Support for Kuka offline programming
- Support for Reis offline programming