EFRE Europäischer Fonds für regionale Entwicklung
Die folgenden Projekte werden aus EFRE-Mitteln gefördert. Das Fachgebiet Füge- und Schweißtechnik bedankt sich beim Fördergeber für die Möglichkeit zur Realisierung der Forschungsvorhaben.
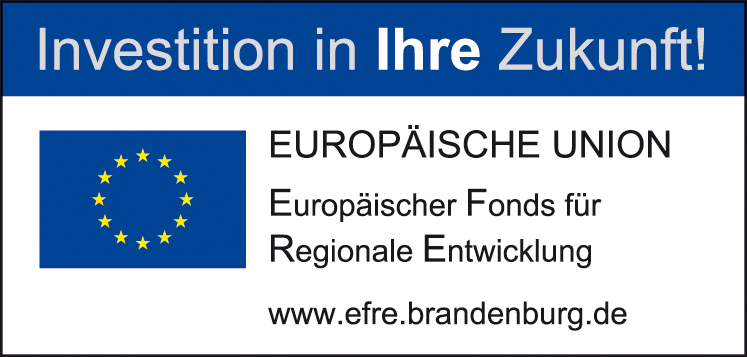
Gasanalyse in der Werkstoff- und Fertigungskette von additiv gefertigten, gefügten und reparierten Hochleistungskomponenten der Energie- und Transporttechnik
Mit dem Vorhaben wird ein Gasanalysesystem für Wasserstoff, Sauerstoff und Stickstoff in die Prozesskette des Fügens, der additiven Fertigung und der Reparatur implementiert. Damit soll das Vorhaben die technischen Grenzen der Fertigungsprozesse erweitern und gleichzeitig die Qualität, Effizienz und Nachhaltigkeit der Werkstoffe erhöhen. Die Kenntnis der Gaskonzentrationen in Werkstoffen ist entscheidend für die Auslegung und Optimierung der Eigenschaften und einer angepassten Verarbeitung.
Grüner Laser als effizientes Werkzeug für ressourcenschonende Technologien – Green to Green
Innerhalb des beantragten Vorhabens soll der bereits bestehende Bereich der Lasertechnik am Lehrstuhl Füge- und Schweißtechnik der BTU mit einem grünen Laser erweitert werden, um hochreflektierende Werkstoffe wie Kupfer- und Bronzelegierungen für Funktionsbauteile mit dem primären Hinblick auf die Elektromobilität und Energieerzeugung verarbeiten zu können. Der Schwerpunkt der Forschung liegt auf Neuentwicklung bzw. Übertragung von elektrisch leitfähigen Funktionsbauteilen aus Kupferlegierungen und der Simulation der gesamten Prozesskette. Ein weiterer wesentlicher Schwerpunkt neben der Funktionsintegration liegt in der stetigen Umsetzung von Leichtbaukonzepten unter Berücksichtigung der Funktionalität.
Erweiterung eines Simulations- und Prüfzentrums für das Generieren, Fügen und Reparieren von Hocheffizienzwerkstoffen - HighMatPro
Aufgrund von zunehmend komplexen Legierungszusammensetzungen, Mikrostrukturen und Herstellungsverfahren ergeben sich erhebliche Herausforderungen für die Verarbeitung von Hochleistungswerkstoffen, insbesondere bei thermomechanischen Prozessen wie dem Fügen, Generieren, Beschichten und Reparieren. Durch das am Lehrstuhl Füge- und Schweißtechnik der BTU Cottbus-Senftenberg betriebene Simulations- und Prüfzentrum Gleeble 3500 können Verarbeitungsprozesse in besonderer Qualität erforscht werden. Das System bietet die Möglichkeit der hochpräzisen physikalischen Simulation von thermischen und mechanischen Vorgängen an definierten Probenkörpern. Erkenntnisse des Laborversuchs können so direkt auf Fertigungsprozesse übertragen werden. Im Rahmen der EFRE-Förderung wird das Simulations- und Prüfzentrum für die Untersuchung von Hochleistungswerkstoffen in Energie- und Transportsystemen zukunftsfähig ausgerichtet. Dafür wird das Zentrum mit berührungsloser Messtechnik zur Temperatur- und Dehnungsbestimmung erweitert. Die in einem geschlossenen Steuer- und Regelkreis integrierte Sensorik und Messdatenerfassung bildet die Grundlage für die exakte Simulation der charakteristischen Merkmale moderner Verarbeitungsprozesse.
smart nanoCOOLing - Entwicklung von hocheffektiven smarten Kühlkörpern auf Basis von nanomodifizierten Werkstoffsystemen für die e-Mobility der Zukunft
Elektronische Hochleistungsbauteile bilden die Kernelemente einer zunehmend digitalisierten Energietechnik und besonders in der Elektromobilität. Ihrer Funktionseffizienz kommt in den nächsten Jahren eine stetig wachsende Bedeutung zu. Die Bauteileigenschaften beeinflussen wesentlich die Verluste bei der Umwandlung der elektrischen Energie und die dabei entstehende Wärme. Das vorgestellte Vorhaben zielt auf die Herstellung von ultraeffizienten sowie thermisch und mechanisch hochbelastbaren Kühlkörpern. Durch die Kombination der additiven Fertigung zur Umsetzung komplexer, innerer Kühlstrukturen sowie beanspruchbaren, nanoverstärkten Werkstoffsystemen mit höchster Wärmeleitfähigkeit soll eine neue Klasse von Kühlkörpern designt und serientauglich realisiert werden.
i-flow - Effizienzsteigerung von Festoxidbrennstoffzellen durch Infiltration und Optimierung der Strömungskennwerte
Im Rahmen dieses Forschungsprojektes wird das Ziel der Effizienzsteigerung von Hochtemperaturbrennstoffzellen (SOFC) verfolgt. Durch lokale Infiltration der Einzelzellen, die aus keramischen und metallischen Werkstoffen gefertigt sind, soll bei minimaler Beeinflussung der Gasdiffusion und -strömung die elektrische und thermische Kontaktierung verbessert werden, sowie die mechanische Beanspruchung von Anode bzw. Kathode im Kontaktbereich reduziert werden. Eine geometrische Optimierung der zellverbindenden metallischen Bipolarplatten, welche eine Trennung und Durchströmung der Prozessgase Wasserstoff und Sauerstoff gewährleisten, soll zudem zur Steigerung des Wirkungsgrades gegenüber konventionellen SOFC beitragen. Komplexe Geometrien werden durch den Einsatz additiver Fertigungsverfahren, wie beispielsweise dem selektive Laserschmelzverfahren, ermöglicht. | Poster |
mediStent - Additive Fertigung medizinischer Koronarstents zur Behandlung von Arteriosklerose
Das Ziel des Forschungsvorhabens besteht in der Entwicklung additiv gefertigter Stents für die Anwendung als medizinische Implantate, der benötigten Werkstoffe sowie der zugehörigen System- und Prüftechnologien zur effizienten und ressourcenschonenden Herstellung. Hierzu werden die 3D-Druckverfahren selektive Laserschmelzverfahren (SLM®) und das Fused Deposition Modeling Verfahren (FDM) zur Umsetzung filigraner, komplexer Stentstrukturen mit anforderungsgerechten mechanischen Eigenschaften weiterentwickelt. Durch die Herstellung neuartiger Metallpulver durch Verdüsung und spezieller polymergebundener Metallfilamente mittels Compoundierung, wird das Anwendungsspektrum in der Medizintechnik erweitert. Die gezielte Auslegung der additiven Fertigungsverfahren, eine anforderungsgerechte Spezifikation des Sinterprozesses sowie eine Weiterentwicklung der elektrochemischen Politur ermöglichen hierbei die definierte Einstellung der mechanischen Eigenschaften sowie die Umsetzung hoch filigraner Stentstrukturen.
Material- und ressourceneffizientere Prozessketten durch Kombination von Umformverfahren und additiver Fertigung
Das Hauptziel des geplanten Projektes ist die Entwicklung effizienter Prozessketten durch Kombination umformender und additiver Fertigungsverfahren, um großvolumige Bauteile mit komplexen Geometrien in Kleinserien oder als Einzelteil wirtschaftlich herzustellen. Die Verfahrenskombinationen gestatten infolge der Aufsummierung der jeweils technologischen Vorteile die ressourcenschonende Fertigung von hoch beanspruchten Bauteilen, deren Abmessungen nicht durch Einschränkungen der additiven Fertigung begrenzt sind. | Poster |
Im Rahmen des Forschungsvorhabens werden folgende Forschungsschwerpunkte bearbeitet:
- Experimentelle Untersuchungen zur Integration von additiven Fertigungsverfahren insbesondere dem Laserstrahl-Auftragschweißen in umformtechnische Prozessketten
- Numerische Prozesssimulation des Laserstrahl-Auftragschweißens
- sowie die Herstellung vom Demonstratoren
Ressourceneffiziente Leichtbauweisen aus metallischen Werkstoffen durch generatives, selektives Laserstrahlschmelzen
Innerhalb des Vorhabens soll die Werkstoff- und Fertigungsforschung an der BTU Cottbus – Senftenberg um das innovative und zukunftsweisende Verfahren, dem selektiven Laserstrahlschmelzen, erweitert werden. Das Verfahren zählt zu den pulverbettbasierenden generativen Verfahren, mit dem sich sehr komplexe und filigrane Strukturen mit minimalen Wandstärken und sehr guten Oberflächenqualitäten werkzeuglos herstellen lassen. Komplexe Leichtbauweisen, die in den meisten Fällen dreidimensionale Strukturen (z. B. Gitter-, strukturierte-dünnwandige und makroporöse Strukturen) aufweisen, besitzen einen großen Potential und vielseitige Anwendungsmöglichkeiten, wie zum Beispiel für den Fahrzeug-, Maschinen- und Energieanlagenbau und auch für energietechnische Apparaturen (Katalysatoren, Wärmetauscher und Reaktoren). Die Entwicklungen adressieren Anforderungen hinsichtlich komplexer, funktionsintegrierter, gewichtsoptimierter Leichtbaulösungen aus metallischen Werkstoffen.
Herstellung und Fügen von energieeffizienten hybriden Faser-Kunststoff/Metall-Mehrschichtverbunden
Eine neue Generation von Leichtbauhalbzeugen kombiniert dünne thermoplastische Kunststoffschichten und metallischen Einzellagen zu einem hybriden Mehrschichtverbund mit hervorragenden Fertigungs- und Systemeigenschaften. Sie stellen eine vielversprechende Alternative für den Fahrzeugbau dar. Insbesondere die noch relativ junge Werkstoffgruppe der textilverstärkten thermoplastischen Kunststoffe bietet für den Einsatz in hybriden Mehrschichtverbunden wesentliche Vorteile, was vor allem in den kurzen Zykluszeiten bei der Bauteilherstellung und der Verwendung von kostengünstigen thermoplastischen Kunststoffsystemen begründet liegt.
Das Ziel des Projektes besteht daher in der Auslegung einer effizienten Herstellung und Verarbeitung von hybriden FK/M-Mehrschichtverbundhalbzeugen, welche die Voraussetzungen für den Einsatz in der Großserie schafft.