Determination of material parameters
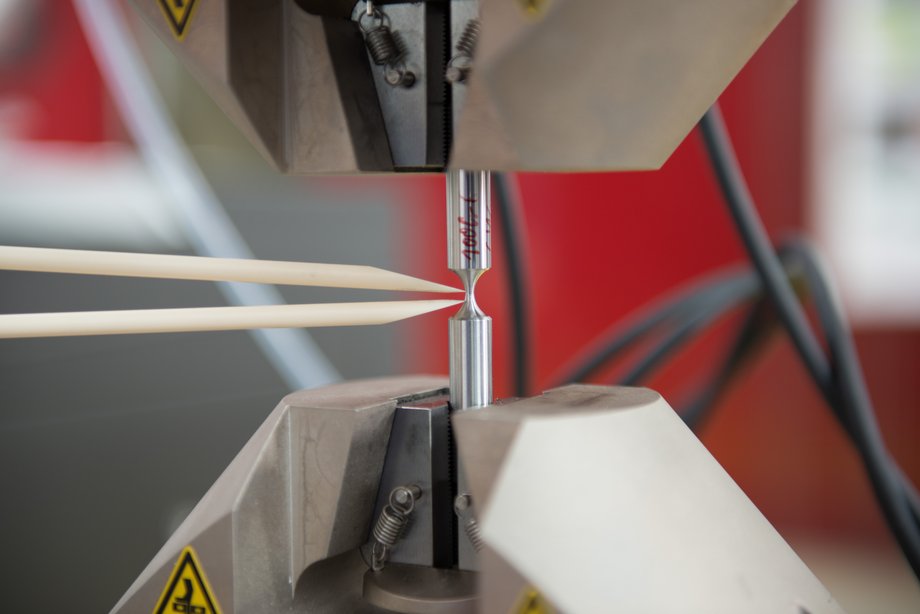
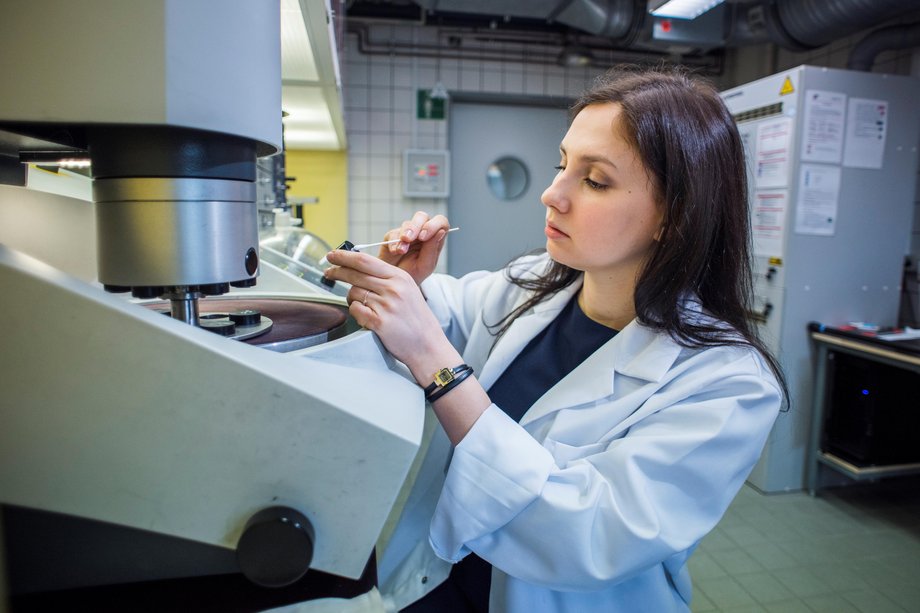
Fields of application
- Determination of temperature-dependent material characteristics in hot tensile tests for numerical simulation
- Characteristic values: proof stress, tensile strength, elongation at break
- Temperature range 20 - 1500 °C by controlled inductive heating
- Fast, joining process specific specimen heating
- Optimal temperature distribution in different specimen geometries by adapted induction coils
- Temperature and strain rate dependent material characteristics
HF generator AXIO 5/450 T for inductive specimen heating
- Power 5 kW
- Frequency range 50 - 450 kHz
- High efficiency due to optimum operating frequency
- Acquisition of all process parameters
High-temperature extensometer for strain measurement on the sample
- Measuring principle: inductive transformer
- Measuring length: 4 - 50 mm
- Measuring path: 10 mm
- Resolution: 0.1 mm - 130 mm
Drop tower CEAST 9350
- For notched bar impact test and puncture test
- As well as device for Tensil Test
- Max test speed 24m/s or 1800 Joule
Walter and Bei universal testing machine
- Servo-hydraulic universal testing machine
- With high resolution digital controller PCS5000 and testing software DION-Pro
- Max test force 150kN
Physical or experimental simulation of manufacturing processes
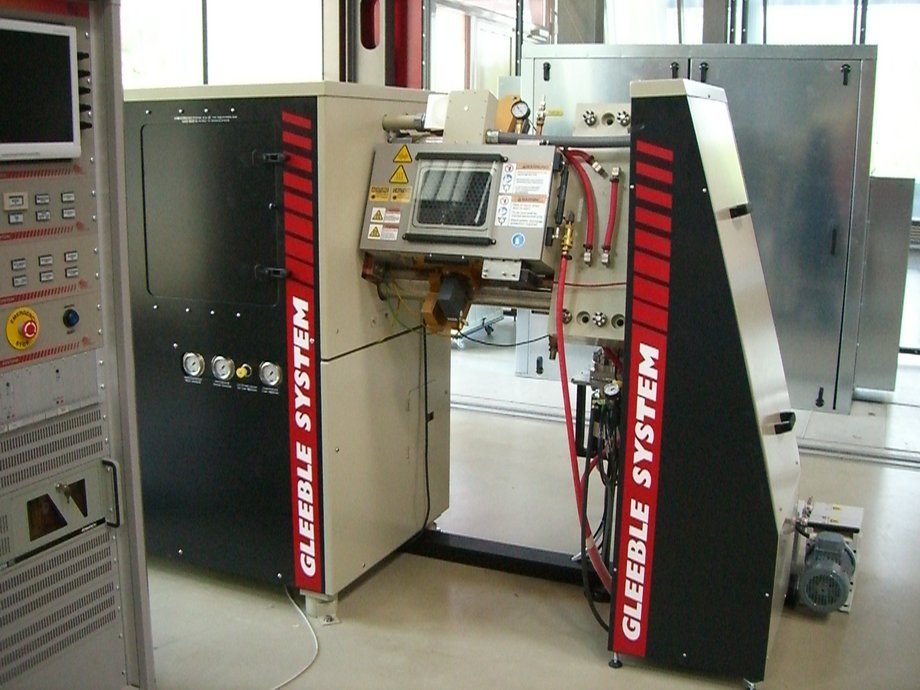
Fields of application
Processes
- Welding
- Forming
- Forming
- Forging
- Heat treatment
Material processes
- Melting and solidification
- Recrystallization
- Transformation behaviour and plasticity
- Precipitation behaviour
- Mechanical hardening
- Relaxation
- Hot cracking tendency
- Cold cracking tendency
Material testing
- Continuous and isothermal ZTA, ZTU, STAAZ charts
- Thermal expansion
- Stress-strain diagrams (tension/compression)
- Creep curves
- Thermal/mechanical fatigue
- Critical strain rate for hot cracking
Gleeble 3500
Features
- Complex system for physical simulation of thermo-mechanical processes as well as for quasi-static, dynamic and cyclic testing
- Synchronous digital control and acquisition of temperature, displacement, strain and force
- Exact time reproduction of thermal and mechanical loads on specimens and components
- Simulation corresponds to the real loading of the material during the manufacturing process or in operation
Technical data
- Temperature range 20 - 1700 °C
- Heating and cooling rates up to 10000 °C/s
- Maximum force 98 kN
- Maximum test speed 1000 mm/s
- Vacuum and controlled atmosphere
Hydrogen analysis
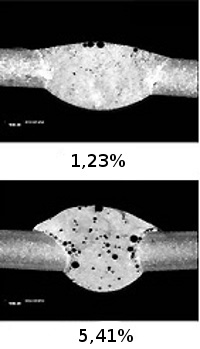
Areas of application
- Materials: steel, non-ferrous metals, e.g. Al and its alloys, Al die casting
- Welding consumables
- Metal powder
- Welds
- Coatings
- Customer specific analysis requirements
Hydrogen analyzer H-mat 225
- Melt extraction furnace with freely selectable analysis temperature up to
- Approx. 2500 °C for the determination of the total hydrogen content
- Infrared furnace for the determination of diffusible hydrogen by artificial ageing up to 900 °C
- Rapid analysis, automatic sequence
- Highly stable detection system with automatic measuring range selection
- Optical temperature measurement and control
- Measuring range: 0.1 - 1000 ppm
- Resolution: 0.01 ppm
Three-dimensional distortion measurement
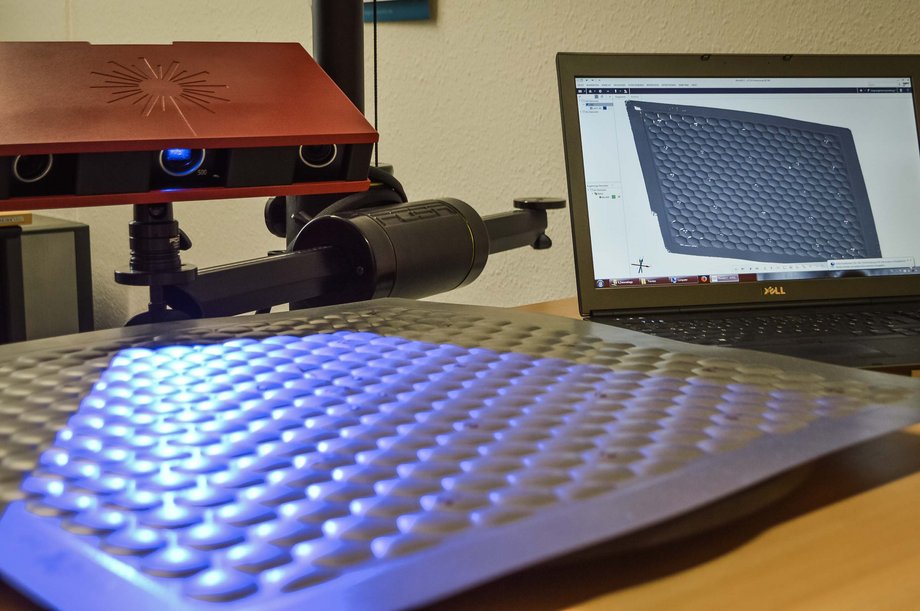
Application areas
- Deformation measurement on complex real components during the manufacturing process
- Manufacturing process, e.g. during joining
- Material testing
- Strength assessment
- Verification of FE simulations
- Analysis of the deformation behavior of homogeneous and inhomogeneous materials
- Materials, e.g. weld seams
- Strain calculation
Surface deformation measurement system ARAMIS®
- Surface with stochastic pattern
- Online image recording with digital 3D camera system
- Recordings in defined time intervals
- Offline evaluation or calculation of displacements
- Surface and graphical representation of the measurement results in the three-dimensional result space with high measurement point density. The graphical representation of the measurement results enables an optimal understanding of the component behaviour
Area hardness measurement
Areas of application
- Hardness scans of surfaces, e.g. welding seams
- Line scans
- Hardness of indentation, edge hardness and nitriding hardness
- Depth measurements according to DIN 50190
- Serial measurements
- Multiple measurements (several Eht, Rht, Nht or line measurements are carried out one after the other)
Hardness scanner UT 100
- Test load from HV 0.1 to HV 2
- Vickers hardness measurements according to DIN 50133
- Vickers hardness measurements with the UCI method according to VDI/VDE guideline 2616
- Hardness values in HV, HRC, HB or tensile strength (conversion according to DIN 50150)
- Positioning accuracy 0.01 mm
- Travel 270 x 290 x 130 mm
Area temperature measurement
Application areas
- Measurement of temperature fields during joining
- Temperature measurement
Thermography system "Vario CAM hr research
- Wavelength: 7.5 - 14 µm
- Measuring range: -40°C ... +1200°C
- Measuring accuracy: ±1.5K (0°C ... +100°C, otherwise ±2K or 2%)
High-speed systems
High speed camera
Photron Fastcam SA5 with Cavilux HF laser light
- 1024 x 1024 pixel up to 7.000 frames / second
- Up to 1.000.000 frames / second at reduced resolution
- 16GB memory