Nano-Electrostatic Drive Valve And Micropump (NED-VAMP)
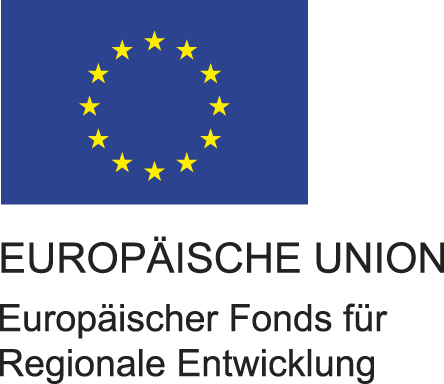
Name:
"Nano-Electrostatic Drive Valve And Micropump"
Active Fluidic Microdevices (micropump and microvalve) with an actuation part based on NED principle
Funding:
This project is financially supported by the European Regional Development Fund (ERDF).
Motivation:
Fluidic systems are a key component of the development of complex systems. Various domains of industry such as biotechnological, pharmaceutical or automation industry, require miniaturized components that can achieve basic fluidic operations(flow generation or regulation) in order to
achieve process requirements constrained by a logic of short response time, high precision, minimal footprint, and low consumption. The NED-VAMP project will produce components that will respond to the previously stated requirement and give the possibility of new paradigm for industry.
Approach:
The fluidic systems are based on a new technology developed and patented by Fraunhofer Institute for Photonic Microsystems IPMS. MEMS actuator, based on the generation electrostatic forces, can, under electrical potential, change the shape from straight to cylindrically curved. The integration of those actuators as active walls into closed cavities gives the opportunity to interact efficiently with the fluid. This approach permits to access a new level of freedom in a logic of forms and integration of components for the engineering and the design of fluidic components.
Details:
Based on the simple electrostatic process, the 2.5D components are micro-machined from the surface in the depth of the bulk silicon. The fabricated actuators as well as the active fluidic layer can be meticulously designed and optimized in order to achieve the best transfer of the mechanical structure to the fluid. The components based of such a technology will take advantage of those engineering steps, authorizing more complex structuration.
Aim:
The principal goal of NED-VAMP is to validate the concept of fluidic components using NED as actuating principal. In order to achieve that task, MEMS test structures achieving flow establishment (micropump) as well as flow regulation (microvalve) will be designed, and fabricated for the aim of the project. As a following step, those components will be tested under varying pressure in order to evaluate their flow response. The combination of components (multiple micropumps working in parallel, combined with valves) will also be implemented to achieve more complex operation (multiphase, concentration gradient, droplet dispenser) to evaluate the components in real conditions.
Project duration: 10/01/2016 - 01/31/2019