Laboratory Research Facilities
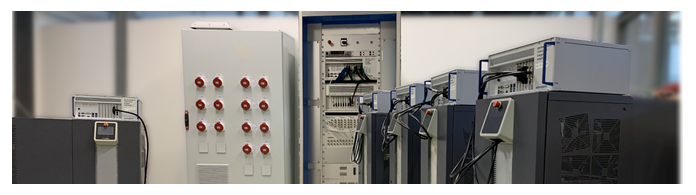
Experimental performance demonstration and validation is fundamental for the successful transfer of new control engineering solutions into application. Likewise, experiments often inspire new theoretical developments and problem statements. To support these aspects, our group has implemented flexible and fast reconfigurable laboratory environments for hardware-in-the-loop (HiL) and power-HiL (PHiL) testing.
Furthermore we have a drone laboratory to test and validation of control algorithms in respect to interaction of drones together and with their environment.
If you are interested in using these facilities for your own research or study purposes, please feel free to contact us via fg-regelungssysteme(at)b-tu.de.
Power-hardware-in-the-loop testbed for intelligent operation and control of low-inertia power systems
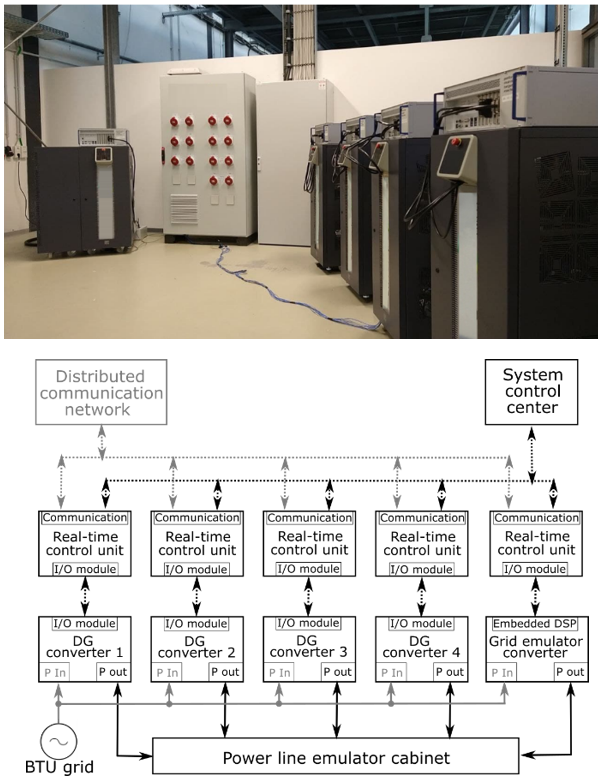
The worldwide usage of renewable sources has remarkably increased in recent years in order to reduce fossil fuel consumption in the area of energy systems. A key aspect of this transition is the integration of a larger number of inverter-based distributed generation (DG) units based on renewable sources. The physical differences between inverter-based DGs and conventional fossil fuel-driven rotating machines imply a reduction in the overall power system inertia, thus potentially decreasing the system robustness against disturbances. Such power systems with a high share of inverter-based DGs and loads are therefore commonly termed low-inertia power systems.
The new structural and dynamical properties of low-inertia power systems result in the need for novel intelligent control and operation strategies suitably tailored to such systems. An important aspect thereby is that due to these substantial changes in the system properties, the mere usage of simulation-based studies for performance demonstration and validation of new control and operational schemes may often be insufficient.
To address this challenge, we have developed a power-hardware-in-the-loop (PHiL) testbed for low-inertia power systems (230/400VAC, 750VDC, 110kW) that combines a real-time simulation platform with actual electrical hardware (see right figure above). The testbed is primarily designed for research purposes, but is also integrated in our teaching activities.
Our PHiL system is fed by the local BTU grid and has a total installed power of 110 kW. The main features of the system are:
- Available hardware: 1x50 kW grid emulator unit, 4x15 kW DG units and a power line emulator cabinet. The GE and every DG unit comprises a three-phase four-wire AC/DC-DC/AC bidirectional converter.
- Simulation/control platform: The measurement, communication and control processes of each converter are executed by a real-time control unit (see right figure above). All control units are fully compatible with Matlab/Simulink models for design and validation of control algorithms.
- Flexible operation: The grid emulator and DG units can adopt a single-phase or three-phase converter configuration in both the AC or DC setting.
- Flexible topology: The power line cabinet allows to construct different network topologies as well as to emulate single-phase and three-phase short circuit events.
- Accessibility to low-level controllers: The DG units are specifically designed such that both high- and low-level control layers of the AC/DC (rectifier) and DC/AC (inverter) stages can be accessed and modified.
- Emulation of large-scale networks: The grid emulator unit is a programmable power amplifier able to emulate dynamics, disturbances and fluctuations commonly found in large scale power systems.
Hardware-in-the-loop test and validation environment for modern automation and control solutions
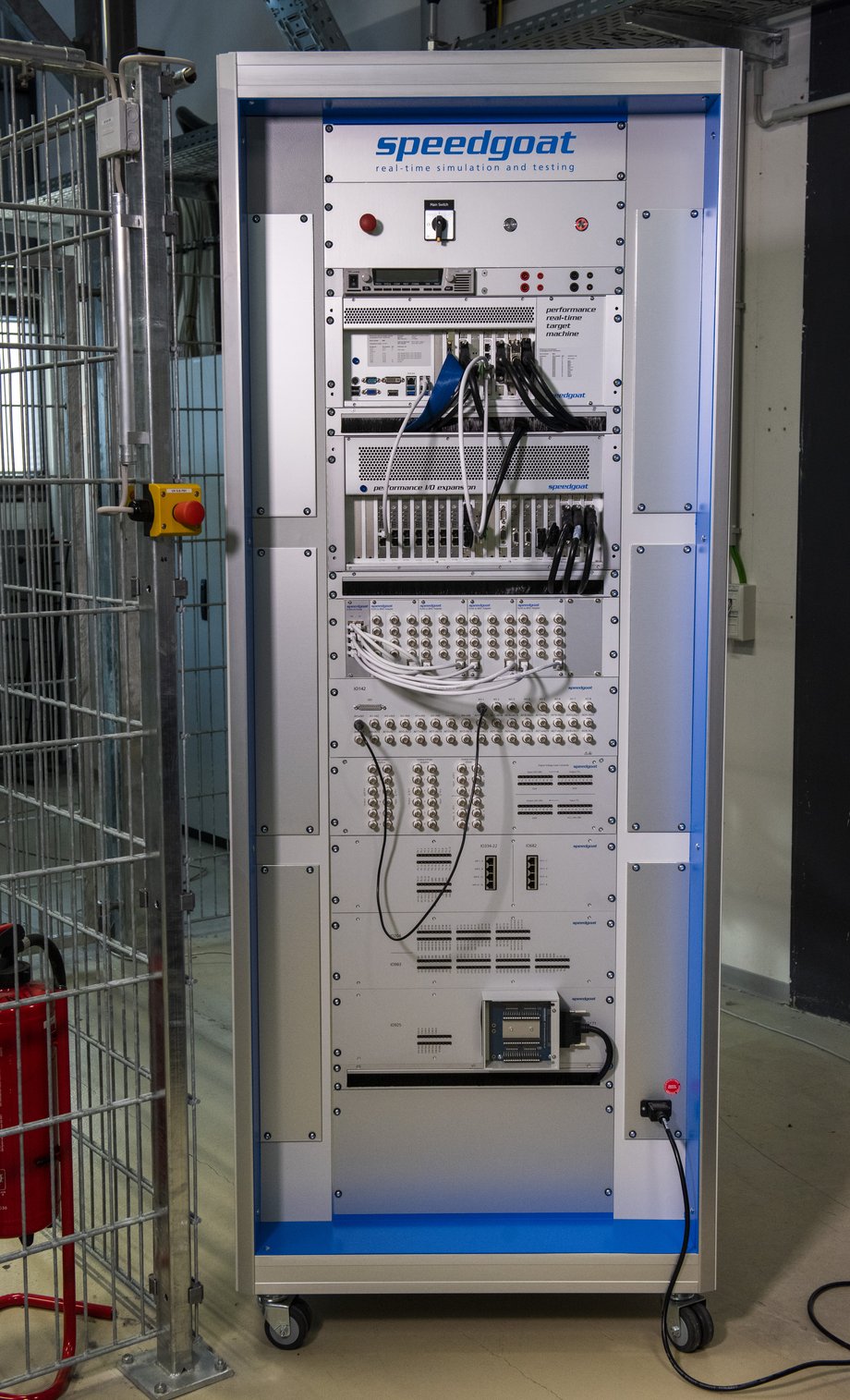
Our Hardware-in-the-Loop (HiL) platform consists of an integrated rack system combining a high-performance real-time computing system and several I/O modules with corresponding signal processing. The real-time computing system enables the realistic and reproducible emulation of the actual plant behavior by means of software models (digital twins). Programming can be done directly in Matlab/Simulink. Due to the HiL approach, its use is not limited to a single field of application, but encompasses various promising areas, such as Industry 4.0, rail and freight transport, and (hybrid-electric) aviation. In this context, the HiL platform enables versatile, user-friendly development and test processes that enable an efficient workflow and rapid implementation of modern automation solutions. Wireless sensors are used to represent networked systems (e.g. position, energy consumption, temperature ...). The platform has I/O modules with support for various industrial protocols (including Profibus, Profinet, Modbus, CAN, ARNIC, MVB). This enables fast, uncomplicated connection of electronic control units (ECUs) and programmable logic controllers (PLCs).
Some key features of the system are:
- Real-time computer
- 32 analog inputs + 8 analog outputs + 24 digital I/O
- Kintex 7 325k programmable FPGA
- Industrial protocols: Profibus, Profinet, Modbus, CAN, ARNIC, MVB
Drone lab to test and validation of control algorithms
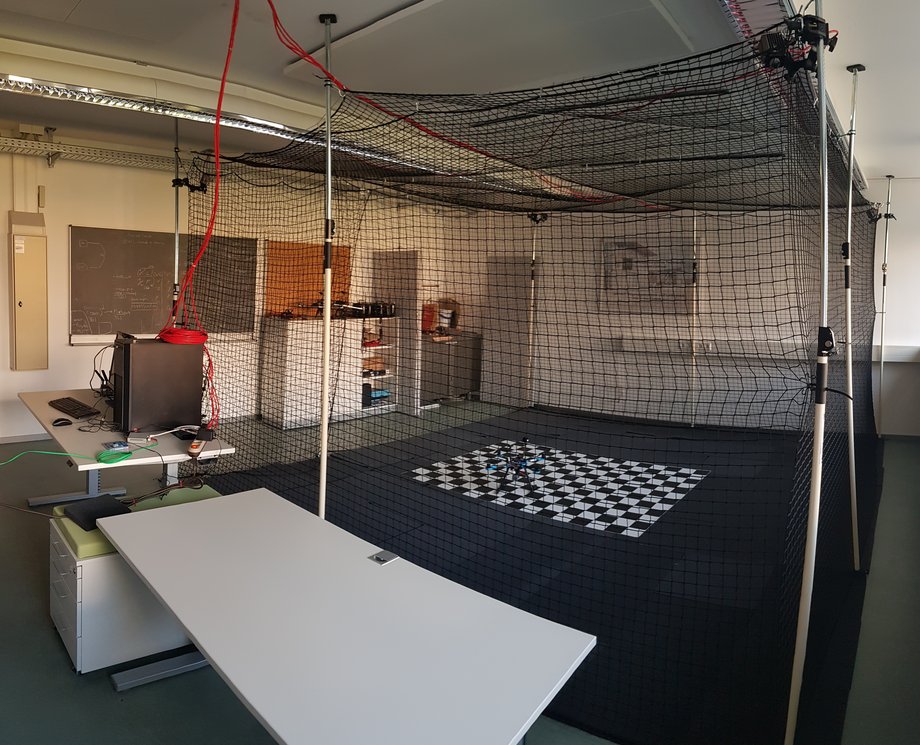
The drones laboratory form part of the department of Control Systems and Network Control Technology at BTU. In this lab the students can carry out research on control over unmanned aerial vehicles (UAVs) with state of the art technology for the detection of the position of the UAV in a controlled environment.
Activities
The lab is used for MSc thesis and for the complementary practical part of the following courses of the department: "Project Laboratory of Control Systems and Network Technology" and "Control Engineering 1”.
Research Topics of Interest
- Time delay in Multi-agent systems
- Integration of UAVs with 5G communication technology
- High level control under ROS framework for real applications
- Parameter estimation in real time
Motion Capture System
- OptiTrack Prime 13 cameras, with 1.3MP resolution, 240 fps frame rate and 4.2 ms latency
- The flying workplace protected by the net is 4x4x2 m.
Current Vehicles
- Several parrot mambo drones
- 6 pixhawk controlled drones with incorporated GPS
Communiction
- Wifi
- 5G standalone communication
Industrial and Academic Projects
- iCampus-5G connected sensing (2024-2026)
Show and evaluate the advantages of using 5G communication in different industrial applications. As a showcase example, we use UAVs under different indoor scenarios. - 5G Waldwächter project (2022-2024)
To enable a set of UAVs with the open architecture capable of supporting in the wildfires detection in the south of Cottbus. The outdoors flights can be combined with indoor previous tests. - iCampus-upwards project (2022-2023)
To create solutions for the collision avoidance technics implemented in indoors and outdoors environments.
People
Cooperations
- S. Auer, elena international
- D. Efimov, INRIA, France
- J. Kurths, F. Hellmann and M. Anvari, PIK, Germany
- J. Raisch, C. Hans and Lia Strenge, TU Berlin, Germany
Funding
- German Research Foundation (DFG)
- German Federal Ministry for Economic Affairs and Climate Action (BMWK)
- Federal Ministry of Education and Research (BMBF)
- European Regional Development Fund (ERDF)
European Regional Development Fund (ERDF) via Project “INES”
Selected publications
A. Krishna, I. Jaramillo-Cajica, S. Auer and J. Schiffer
"A power-hardware-in-the-loop testbed for intelligent operation and control of low-inertia power systems" Automatisierungstechnik, 70, no. 12, pp. 1084-1095, 2022
doi