Hier finden Sie eine Übersicht der Promtionsthemen und weitere Informationen zu den Betreuungs-Tandems (BTU & BAM).
PhD Topic 1 – Novel materials and coatings for the detection of hydrogen and hydrocarbons Lead: BTU
BTU | BAM |
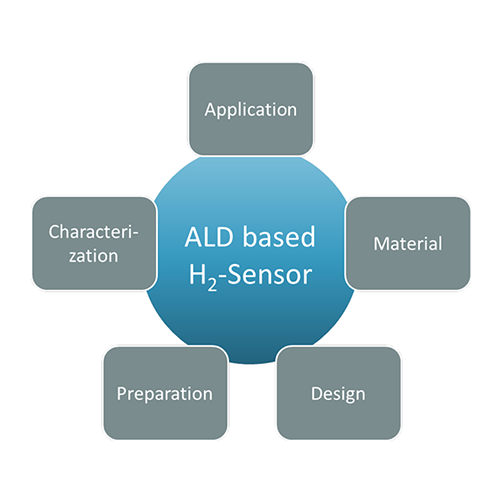
Atomic layer deposition (ALD) is a very promising route to manufacture chemical sensors due to a very high degree of precision with respect to chemical composition and morphology of the active sensor’s surface. The key for using this technology to develop efficient sensor materials for selective and sensitive detection of hydrogen lies in the optimization of this method by applying different analytical tools (e.g., X-ray photoelectron spectroscopy, time-of-flight secondary ion mass spectrometry, focused ion beam and electron microscopy) as part of developing the synthesis process.
The aim of this project is to gain an insight into the materials properties and synthesis process by a unique combination of surface sensitive methods. This insight will allow the characterization of the nucleation and growth process, which needs to be adapted carefully as the materials properties are strongly dependent on the specific choice of precursors employed and their chemical reaction with the substrate as well as remaining contaminants, which might lower the efficiency of the final product. To complement the deposition and analysis techniques, kinetic Monte Carlo (kMC) modelling will accompany the present work. KMC methods are particularly suitable to model ALD processes as the microscopic lattice structure and atomic interactions, as well as microscopic film growth processes are accounted for. When opting for a proper lattice Monte Carlo Model, statements can be made concerning the deposition conditions, the chemical composition of the thin layer, as well as of the surface morphology.
The project is structured as a complete R&D process from production to testing thanks to the collaboration between experts from both BTU Cottbus and BAM and the utilization of state-of-the-art facilities in both institutes.
Deliverables:
- ALD preparation recipes for the deposition of metal oxide layers tailored to specific sensor requirements
- Dissemination of characterization and knowledge about the gas-oxide interaction depending on external variables (temperature, pressure, gas composition)
- Detailed assessment of the sensor response depending on gas composition and exposure
Rudi Tschammer
Fachgebiet Angewandte Physik und Halbleiterspektroskopie, Fakultät 1, BTU
E-Mail: Rudi.Tschammer(at)b-tu.de
Kurz-Vita:
Rudi Tschammer was born and raised in Lübbenau/Spreewald, close to Cottbus, and completed his Bachelor of Science in Physics at BTU Cottbus-Senftenberg in 2020. The subsequent Master of Science in Physics has been granted in late 2022 by BTU Cottbus-Senftenberg as well, with a focus on surface physics and catalysis, culminating in the thesis “Structural and chemical characterization of cerium oxide nanoparticles grown on the Au(111) surface” and several beamtimes at different synchrotron facilities, as well as research stays at the University of Bremen (Bremen, Germany) and Brookhaven National Laboratory (New York, USA). Since January 2023, Rudi Tschammer has been a PhD student at the chair of Applied Physics and Semiconductor Spectroscopy, investigating the properties of different oxide thin films deposited by Atomic Layer Deposition (ALD) as well as model catalysts based on rare-earth metal oxides.
Kontakt
Prof. Dr. Jan Ingo Flege
Fachgebiet Angewandte Physik und Halbleiterspektroskopie, Fakultät 1
E flege(at)b-tu.de
T +49 (0)355 69 5352
PhD Topic 2 – Evaluation of the influence of lubricants on pre-ignition of hydrogen for engine relevant conditions Lead: BTU
The operation of gas engines with green hydrogen from renewable energy sources is a future technology to achieve CO2-neutrality in the energy and transport sector. To increase the thermal efficiency of such piston engines the increase of compression ratio and charging of the intake air are applied. This leads to higher compression pressures and temperatures during the engine operation cycle. Further, to avoid galling and excess thermal stresses of the piston rings and cylinder surfaces, lubricating oils are necessary.
Due to the higher thermal auto-ignition propensity of engine oils compared to hydrogen, the oil can cause self-ignition under certain conditions, leading to low-speed pre-ignition (LSPI) phenomena. The LSPI creates strong pressure gradients within the combustion chamber, which can destroy the components, such as piston and valves. For example, low oil viscosities and high calcium content could enhance high pre-ignition rates. Hence, it is important to improve the knowledge of the impact of lubricant properties on LSPI in hydrogen engines.
In the joint research project between BTU Cottbus-Senftenberg, Chair of “Thermodynamics / Thermal Process Engineering”, and BAM Competence Centre “H2Safety@BAM”, the lubricating oil self-ignition process within hydrogen/air-mixtures will be investigated. Two approaches will be facilitated to investigate the self-ignition process: 1. An experimental investigation of the influence of lubricant oil properties under engine-relevant conditions, 2. A numerical investigation to understand the effects of physical and chemical processes on lubricant oil self-ignition. The results will contribute to the H2 safety for gas engine operation by proposing optimum lubricant properties to avoid LSPI, while ensuring appropriate lubrication.
Deliverables
- Fundamental understanding of the influence of lubricant properties on the pre-ignition in hydrogen/air-mixtures
- Validated detailed kinetic model for prediction of pre-ignition in hydrogen/air mixtures and addition of various lubricants
- Contribution to H2 safety by evaluating optimum properties of lubricants for prevention of pre-ignition in hydrogen engines
Hayat El Harrab
Fachgebiet Thermodynamik/Thermische Verfahrenstechnik, Fakultät 3, BTU
E-Mail: elharhay(at)b-tu.de
Kurz-Vita:
Hayat El Harrab was born in Casablanca, Morocco. In 2017, she obtained her Bachelor's degree in Process Engineering and Industrial Chemistry at the ENS in Rabat. At the end of 2018, she relocated to Germany and completed her Master's degree in Process Technology - Process and Plant Technology at BTU Cottbus-Senftenberg with the thesis titled "Combustion and Emission Prediction of Gasoline, Cyclopentanone and Anisole Blends in Spark Ignition Engine". Since October 2022, she is a PhD student at the Chair of Thermodynamics/Thermal Process Engineering under Prof. Dr.-Ing. Fabian Mauß.
Kontakt
Yvonne Teetzen
Fachgebiet Thermodynamik/Thermische Verfahrenstechnik, Fakultät 3
E yvonne.teetzen(at)b-tu.de
T +49 (0)355 69 2600
PhD Topic 3 – Digital sensor twin for hydrogen applications Lead: BAM
BTU | BAM |
|
The optimisation and validation of the process management of hydrogen plants with sensor technologies is the main goal of the project. For this purpose, sensor networks with digitally supported data mining strategies are to be intelligently designed (keywords: artificial intelligence AI or digital twin). Many sensors / sensor systems are available as basic components for this purpose, which, similar to the human senses, monitor physical and chemical parameters on and in plants. In conjunction with computer systems with sufficient performance, the detection and interpretation of malfunctions and process monitoring is thus guaranteed. The project brings together technologies from different fields (microsensors, especially digital hydrogen selective gas sensors, temperature, and humidity sensors; low-power radio/wired networking; sensor fusion based on artificial intelligence) and integrates them for the first time into sensor nodes for, e. g. H2 plant monitoring at fuelling stations, that are multifunctional and offer a constant expansion of their functional spectrum through the learning of signal patterns. Since the project is stepping on the simulation knowledge and the exact signal patterns and application cases are not known a priori due to a lack of corresponding experience, an early establishment of sensor nodes in the field is indispensable to be able to gather experience and, above all, concrete data, and demonstrate online evaluation of the data patterns in the sensor network to develop a methodological approach for digital twins which.
Deliverables:
- Development of a sensor network concept considering literature research, market and patents survey of commercially available sensor elements and detection systems
- Establishing a sensor node system for monitoring and an apparatus for sensor tests
- Digital twin for the determination of hydrogen in air
- Testing of novel H2 sensitive materials and coatings for the investigation of hydrogen distribution in the sensitive layer with generated test gases (connection to topic of novel sensor materials and coatings)
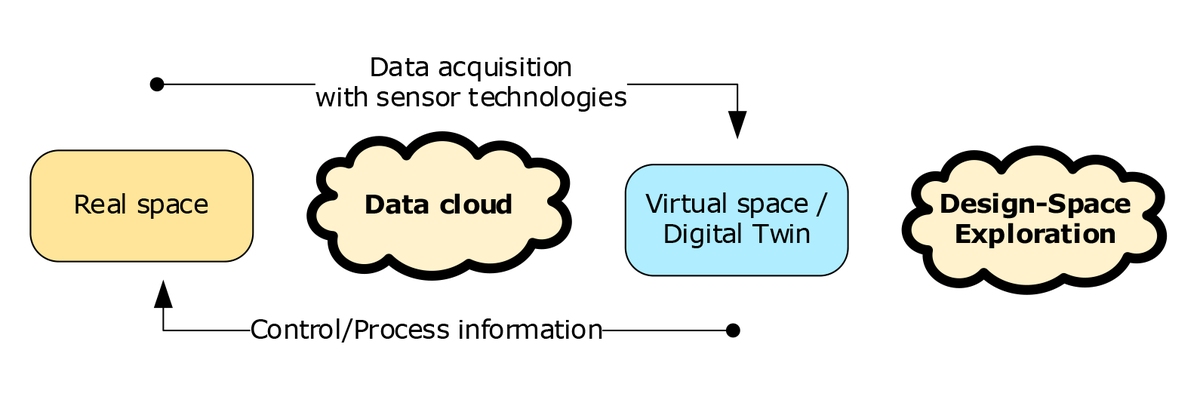
Raduan Sarif
Fachbereich 8.1 Sensorik, mess- und prüftechnische Verfahren, BAM
E-Mail: raduan.sarif(at)bam.de
Kurz-Vita:
Raduan Sarif was born in Noakhali and grew up in Dhaka, Bangladesh. During his school life, He was curious about mathematics and physics, so he joined American International University-Bangladesh (AIUB) and completed his bachelor's in Electrical & Electronics Engineering (EEE) in 2016. After that, he relocated to Germany, where he graduated with a master's degree in Electrical Engineering (EE) from Universität Rostock in 2022. He is particularly interested in researching the system's digital transformation based on sensor technologies and artificial intelligence. His bachelor's thesis was" Designing a Smart Refrigerator," and his master's thesis was "Mobile gas sensing system for the laboratory infrastructure." There he focuses on developing sensor systems and data analysis techniques.
He believes hydrogen will be clean energy for the next generation, helps to keep a pollution-free environment, and build an emission-free planet. So, it is high time to focus on hydrogen safety and digitalization. With interest in the German hydrogen mission, he participates in the BTU-BAM graduate school "Trustworthy Hydrogen" with the responsible topic" Digital sensor twin for hydrogen applications." In October 2022, he moved to Berlin and started his PhD at Bundesanstalt für Materialforschung und -prüfung (BAM) Division 8.1 "Sensors, measurement, and test methods."
Kontakt
Dr. rer. nat. Carlo Tiebe
Fachbereich 8.1 Sensorik, mess- und prüftechnische Verfahren, BAM
E Carlo.Tiebe(at)bam.de
T +49 30 8104-4518
PhD Topic 4 – Influence of manufacturing process-related residual stresses in wound composite material on the operational safety of H2 pressure vessels Lead: BAM
BTU | BAM |
The storage of hydrogen is essential for the successful implementation of the energy transition and emission-free mobility. Modern type IV pressure vessels essentially consist of a polymer liner and a continuous fibre-reinforced composite deposited on the liner. The composite can be created in the pressure vessel using winding technology, the AFP process (Automated Fibre Placement) or by braiding.
During the production process, the fibres must be placed under pretension. Without suitable countermeasures, this leads to a reduction of the originally introduced residual stresses in the winding process layer by layer. As a result, the different layers of the same direction bear unevenly. This leads to reduced strength and reliability. To prevent this, the liner can be supported by internal pressure in such a way that a uniform pretension and load distribution are achieved across the wall thickness.
For a better understanding of the influence of residual stress and the methods of prevention, these two aspects are to be systematically investigated. For this purpose, extensive simulations of the tank wall and hydraulic tests on a series of model tanks are planned. These model tanks are to be designed and manufactured to the pressure level usual for hydrogen itself and equipped with integrated sensors. The tests will be carried out hydraulically and are to be statistically evaluated. The doctoral thesis described in this way is intended to describe the influence of the residual stresses caused by the manufacturing process on the operational safety of H2 storage tanks and concrete approaches for avoiding these imperfections. Within the scope of the described doctoral thesis, it is intended to describe the influence of the residual stresses caused by the manufacturing process on the operational safety of H2 storage systems and to demonstrate an approach for avoiding these imperfections.
Deliverables:
- Description of the FE-model of the model composite pressure vessel including the winding and curing process under consideration of a controlled internal pressure in the liner
- Determination of the design and the manufacturing process (filament winding and AFP process) of model composite pressure vessels including the targeted parameters
- Implementation and application of a suitable test setup with integrated SHM system
- Report on the findings, including the impact of internal stresses by internal pressure on strength and reliability aspects.
Bartosz Popiela
Fachbereich 3.5 Sicherheit von Gasspeichern, BAM
E-Mail: bartosz-maciej.popiela(at)bam.de
Kurz-Vita:
Bartosz Popiela was born in Poznan, Poland. He obtained his Bachelor and Master of Science degrees in Mechanical Engineering from the Technical University of Berlin. In his previous research he focused on structural behaviour of fiber reinforced composites, e.g. repair patches of wind turbine blades or behaviour of anisotropic box beams under torsional loads. Moreover, he developed lightweight concepts for partners from automotive, rail and shipbuilding industries.
In his current research, Bartosz Popiela investigates residual stresses in hydrogen composite pressure vessels as a PhD Student at Division 3.5 “Safety of Gas Storage Systems” of BAM.
Kontakt
Dr.-Ing. Georg Mair
Fachbereich 3.5 Sicherheit von Gasspeichern, BAM
E Georg.Mair(at)bam.de
T +49 30 8104-1324
PhD Topic 5 – Influence of manufacturing-induced imperfections on the operational safety of composite H2 pressure vessels Lead: BTU
BTU | BAM |
The storage of hydrogen is essential for the successful implementation of the energy transition and emission-free mobility. Modern type IV pressure vessels essentially consist of a polymer liner and a continuous fibre-reinforced composite deposited on the liner. The composite can be created in the pressure vessel using winding technology, the AFP process (Automated Fibre Placement) or by braiding.
During the manufacturing process, imperfections are introduced into the composite pressure vessels, which can lead to a significant reduction in operational reliability.
In order to increase the lightweight level of H2 pressure vessels and to increase their reliability, knowledge about the influence of manufacturing imperfections on the operational safety of H2 pressure vessels is essential.
In the joint research project between the BTU-Cottbus, Chair of “Polymer-based Lightweight Design (PbL)” and BAM Divisoon-3.5, “Safety of Gas Storage Systems”, it will be possible to demonstrate the influence of manufacturing-related imperfections as a function of the material combination used on the operational reliability of H2 storage tanks by means of extensive structural tests. The scientific issue is considered using two approaches: The verification of critical, manufacturing-induced imperfections and the derivation of corresponding recommendations for vessel design and manufacturing. In addition, the increase of operational safety through the optimization of a new material combination based on a fracture toughness-modified thermoset matrix system with thereby increased tolerance against damage initiation by manufacturing-induced imperfections.
Deliverables:
- Development and manufacturing (filament winding and AFP process) of a representative composite test specimen with targeted imperfections
- Implementation and application of a suitable test setup with integrated SHM system
- Description of the FE-model of the model composite test specimen including manufacturing-induced imperfections
- Derivation of design rules and new material concepts (fracture toughness modification)
- Report on the findings, including the impact of manufacturing-induced imperfections on the operational safety and Derivation of design rules and material concepts
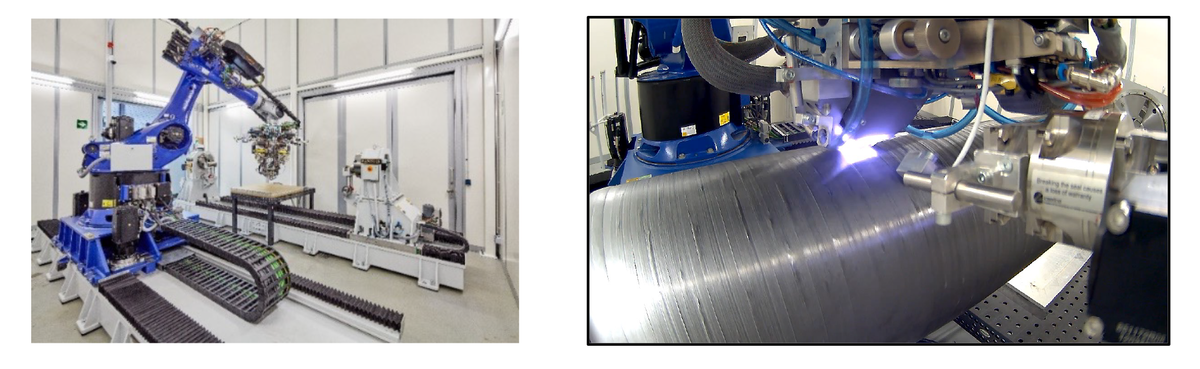
Oliver Dorn
Fachgebiet Polymerbasierter Leichtbau, Fakultät 3, BTU
E-Mail: oliver.dorn(at)b-tu.de
Kurz-Vita:
During my bachelor studies, naval architecture and ocean engineering, I already dealt with advanced engineering issues. Together with the REXUS (21) team UB-SPACE, I was able to launch a rocket into space with a research project in 2017. Driven by lightweight requirements, individually printed (3D printed) polymer bearings were produced here. As a result, we were awarded the Bronze manus® from IGUS as a team.
Driven and inspired by the freedom of construction and the possibilities that anisotropic materials offer, I found my joy in fiber reinforced lightweight materials. I learned the practical knowledge for this already in my bachelor studies. I was able to develop this further in the master's program at Leibnitz University (computer-aided engineering). Part of the master studies was an internship, which I completed at DLR Braunschweig. Here I worked on the programming of a model generator for the three-dimensional modelling of composite scarf joints. Based on this I wrote my master thesis about an alternative approach for the modeling and nonlinear calculation of shaft joints of composite structures.
Subsequently, I spent the next 3 years at the Institute of Statics and Dynamics, where I supervised different projects. I also supervised the composites lab, which dealt with the fabrication of different components and test specimens. Along the way, I manufactured components and prototypes on a 5-axis CNC machine for different student teams at the University of Hannover.
Since green hydrogen holds an incredible potential, I am now happy to be part of the research group and to contribute to the safe production of hydrogen pressure vessels.
Kontakt
Dr.-Ing. Lars Ulke-Winter
Fachgebiet Polymerbasierter Leichtbau, Fakultät 3
E lars.ulke-winter(at)b-tu.de
T +49 (0)355 69 2556
PhD Topic 5 – Influence of fires on tanks for cryogenic fluids Lead: BAM
Liquid hydrogen (LH2) is seen as the most important transport mode on the way to establishing hydrogen (H2) in the energy industry. In addition, LH2 has the long-term potential to become the energy carrier for energy-intensive sectors of the economy, such as heavy-duty transport.
Transport and storage of LH2 occur at temperatures below -240°C and typically at overpressures. The development of suitable systems for this purpose is highly interdisciplinary and involves a great deal of technical effort. Commercial products for this purpose were developed particularly with the mid-20th century emergence of the liquefied natural gas (LNG) market, which requires similar technical solutions. Various suitable technologies were developed, driven by the steadily increasing demand over the last decades and the economic efficiency of the transport systems of LNG.
The situation is different concerning safety. So far, this has only been addressed in a few studies, so there are numerous gaps in knowledge that need to be filled. The focus of the project is to investigate the influence of fires on tanks for cryogenic fluids. For this purpose, research is to be carried out on:
- how fires affect super insulation,
- how fires affect a cryogenic hazardous material in such a tank,
- which models can be used to calculate such incidents.
Aliasghar Hajhariri
Fachbereich 3.2 Gefahrguttanks und Unfallmechanik, BAM
E-Mail: aliasghar.hajhariri(at)bam.de
Kurz-Vita:
Ali is a junior researcher originally from IRAN. He studied for his Bachelor’s in Chemical Engineering and achieved excellent grades. Hence, Ali decided to pursue his passion for research and enrolled for a master’s degree in Chemical and Process Design at Khaje Nassir Toosi University in Tehran. However, he didn't stop at that stage and continued to broaden his research opportunities. In 2017, he pursued a second master’s degree in Chemical and Energy Engineering in Germany at Otto-Von-Guericke University. During his study in Germany, he gained experience in various aspects of industrial studies by doing 2 years of HiWi (Professor Assistant) tasks. Later in 2020, he even worked as a researcher at Otto von Guericke University before embarking on his Ph.D. project at BAM (Federal Institute for Materials Research and Testing). He continuously improves his academic background and experience in research.
Kontakt
Prof. Dr.-Ing. Frank Otremba
Fachbereich 3.2 Gefahrguttanks und Unfallmechanik, BAM
E Frank.Otremba(at)bam.de
T +49 30 8104-1320
PhD Topic 7 – Anion exchange membrane (AEM) water electrolysis for flexible and efficient hydrogen production Lead: BTU
Energy Innovation Centre (EIZ) “Energy Storage and Conversion Laboratory”
The four levels of future sector-coupled energy systems - heat, electricity, storage and mobility - are to be mapped in a CO2-neutral cycle approach based on green hydrogen. At all levels, the corresponding elements of the closed-cycle approach will be developed and optimised, starting from green hydrogen production, followed by further processing of the green hydrogen into synthetic hydrocarbon- and nitrogen-based fuels as well as their storage, transport and conversion into electricity and heat. Each of the four levels is developed using optimisation and digital twin processes in close exchange with fundamental experiments and advanced materials characterisation.
Anion exchange membrane (AEM) water electrolysis for flexible and efficient hydrogen production
As a contribution from the Chair of Thermal Energy Technology, an effective development of the AEM water electrolysis technology will be made on a laboratory scale by carrying out multiscale experiments as well as simulation models to develop and verify a novel AEM water electrolyser concept with noble metal-free catalyst and membrane materials. The degradation behavior of the membrane electrode assembly MEA’s materials will be examined to evaluate the suitability of these materials for industrial AEM electrolysers.
- Present scale (100 cm2).
- Target of EIZ project (360 cm2).
- Long-term stability test (up to 1,000 hours).
Mohamed Elasmar
Fachgebiet Thermische Energietechnik, Fakultät 3, BTU
E-Mail: mohamed.elasmar(at)b-tu.de
Kurz-Vita:
On November 1st 2022, I started a new position as an academic employee in the Chair of Thermal Energy Technology in BTU. The position is based on my master’s degree, which was obtained on July 1st 2022 from the same chair and was mainly relevant to the flexibility modelling and sensitivity analysis of chlor-alkali membrane cells for green hydrogen production. The research work was carried out through a simulation-based approach using MATLAB and Simulink software. Hence, my current task is to convey my modelling expertise of chlor-alkali electrolysis to the recent activities of the chair represented by the alkaline as well as anion-exchange membrane water electrolysis technology.
As an academic staff member, I am one of the BTU’s participants in the project of EIZ-ESEW. In addition, my PhD research topic - Investigation of the performance of an anion exchange membrane (AEM) water electrolyser short stack by representing the spatial flow and temperature distribution in the single cells using a multi-physical AEM model - is registered in the project’s agenda. My research work focuses on simulating the long-term operation of an AEM water electrolyser short stack by developing a physico-chemical model that precisely investigates the performance of the stack. Moreover, the model studies the mass and heat transfer phenomena on a cell as well as a stack level, representing the spatial flow and temperature distribution in the single cells so that critical spots can be detected. Furthermore, the long-term stability of the membrane electrode assembly MEA’s materials will be examined by developing a parametric sensitivity analysis, which identifies the optimum design and operating parameters. In BTU’s Hydrogen Research Centre, multiscale experiments on an AEM water electrolyser test rig will be carried out to examine the performance and the reliability of the model will be evaluated by validating the experimental data.
Univ.-Prof. Dr. Lars Rötzsch
Fachgebiet Thermische Energietechnik, Fakultät 3, BTU
E lars.roentzsch(at)b-tu.de
T +49 355 69 4501