Ergebnisse des Projekts
Im Rahmen dieses Forschungsvorhabens wurde ein gekoppelt analytisch-numerisches Hybridmodell für die Verzugsberechnung von Großstrukturen entwickelt. Um den Anwendungsbereich des Modells zu erweitern, wurde eingangs die Basis der Methode, das analytische Schrumpfkraftmodell, um moderne Schweißverfahren und neue hochfeste Werkstoffe erweitert. Um dem mehr und mehr in den Vordergrund rückenden Leichtbau und die damit einhergehende wachsende Verwendung dünnwandiger Konstruktionen gerecht zu werden, wurde die beim Schweißen auftretenden Instabilitäten untersucht. Das entwickelte Modell ist in der Lage, die Durchbiegung bzw. den Winkelverzuge mit einer hohen Genauigkeit zu berechnen. Die auftretenden Verformungen beim Schweißen von im Raum gekrümmter Trajektorien lassen sich gekoppelt analytisch-numerisch berechnen. Mittels numerischer Untersuchungen und basierend auf den grundlegenden Maximaltemperaturfeldgleichungen wurde in Abhängigkeit der Schweißparameter, Geometrie und Werkstoffkennwerte ein Radius definiert, für den die plastischen Dehnungen einer gekrümmten Trajektorie denen einer geradlinigen entsprechen. Die Verteilung der Wärme in allgemeinen Stoßarten wurde gemäß der reduzierten Dicken und unter Berücksichtigung der entfestigten Zone beim Schweißen im Schrumpfkraftmodell erfasst.
Für die Kopplung des analytischen Modells mit der numerischen FE-Methode wurden elastische Dehnungen gewählt. Die Verifizierung des Kopplungsalgorithmus geschah unter Verwendung ausgewerteter numerisch berechneter Dehnungen. Diese wurden in die Lösungen überführt, die das analytische Schrumpfkraftmodell liefert und anschließend einem der gekoppelten Methode entsprechenden grob vernetzten FE-Modell übergeben und die Verformungen berechnet. Der Vergleich mit durchgehenden thermomechanischen FE-Berechnungen zeigte sehr gute Übereinstimmung. Die Untersuchung der Stabilität und Sensibilität in Form von Netzvariationen im Bereich der eingebrachten Last ergab nur geringe Auswirkungen auf die berechneten Verzüge in der Ebene und im Raum. Nicht konvergierende Berechnungen gab es in keinem Fall.
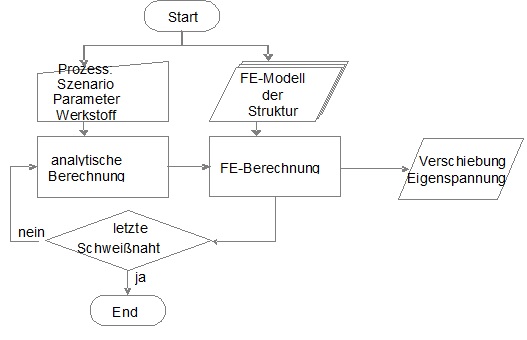
Die Anwendung des gekoppelten Hybridmodells fand zunächst an einfachen elementaren I- und T-Stossverbindungen statt. Die berechneten Verzüge stimmten qualitativ stets mit den Erwartungen und den Experimenten überein, fielen jedoch teilweise zu gering aus. An einer komplexen Struktur, die durch 8 Nähte gefügt wurde, wurde die Berücksichtigung der Schweißreihenfolge im gekoppelten Modell untersucht. Das Hybridmodell ist in der Lage, unterschiedliche Schweißszenarien z. B. Eigenspannungen, die sich bereits im Bereich der Schweißnaht befinden, zu berücksichtigen. Die zweite komplexe Struktur, die berechnet wurde, war eine komplette Decksektion aus dem Schiffbau. Auf eine Grundplatte mit den Abmessungen 16x20m wurden mehrere Profile unterschiedlicher Dicken mittels 88 Schweißnähte gefügt, Abbildung 1. Zum Einsatz kam Laserstrahl-MAG-Schweißen und MAG-Handschweißen.
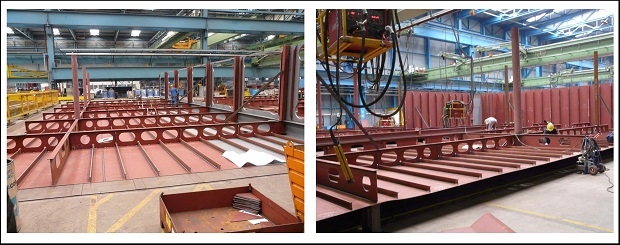
Ein CAD-Modell der Konstruktion wurde von der Meyer Werft GmbH zur Verfügung gestellt und an der Forschungsstelle vernetzt. Die Fertigung der Schiffssektion ist in drei Fertigungsschritte unterteilt, Abbildung 2. Im ersten werden die 24 Deckbalken mittels Laserstrahl-MAG-Hybridschweißen gefügt. Der zweite Fertigungsschritt beinhaltet das Fügen der Unterzüge sowie der Rahmenbalken mittels beidseitigem MAG-Schweißen. Im letzten Fertigungsschritt werden die Kleinteile und die Wände auf die Grundplatte gefügt. Auch hier kommt beidseitig MAG-Schweißen zum Einsatz. Nach jedem Fertigungsschritt wurde die Struktur vermessen und die Verzüge in Längs- und Querrichtung experimentell bestimmt.
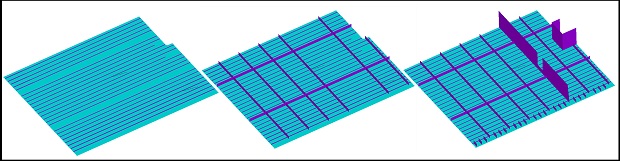
Die berechneten Endverzüge der Schiffssektion, unter Berücksichtigung der unternehmensinternen Schweißanweisungen, stimmen qualitativ mit den erwarteten Verzügen überein, Abbildung 3. Die Verzüge entlang der Seitenränder des Decks wurden experimentell ermittelten Verzügen gegenübergestellt. Es ergab sich quantitative Übereinstimmung in einer sehr guten Näherung, Abbildung 4.
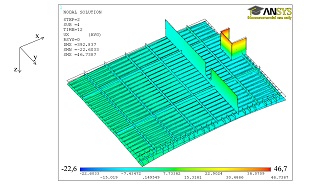

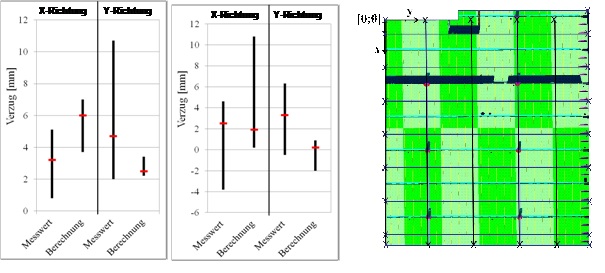
Die CPU-Rechenzeit der numerischen Berechnung an den Großstrukturen betrug in jedem Fall weniger als 10 min pro Fertigungsschritt (4.Kerne-PC). Die Netzerstellung gestaltet sich ebenfalls wesentlich einfacher als bei einer durchgehenden thermomechanischen Schweißsimulation, da der extrem feinvernetzte nahtnahe Bereich sowie die zeitliche Diskretisierung entfällt. Das Modell wurde mit ca. 200 000 Schalenelementen vernetzt und die Verformungen mit jeweils einem Lastschritt berechnet.
Durch den stark reduzierten Modellierungs- und Berechnungsaufwand und die für die Praxis ausreichende Genauigkeit ist das Nutzungspotenzial für die industriellen Anwender inklusive den KMU sehr hoch. Das Modell bietet die Möglichkeit, die Schweißverzugssimulation in der Praxis einzusetzen und diverse Fertigungsschritte bzw. Fertigungsszenerien bereits in der Produktplanung zu analysieren und aus Sicht des Schweißverzugs das Optimum zu bestimmen.
Sind bereits CAD-Modelle der Konstruktionen vorhanden, können diese für die Vernetzung und die anschließende Berechnung der Schweißverformungen genutzt werden. Bestehen bereits vernetzte Modelle, bspw. aus mechanischen Analysen oder Umformsimulationen, gibt es die Möglichkeit, diese direkt für die Anwendung des gekoppelten Hybridmodells zu nutzen.