Aerodynamics
Boundary layer flows
On the influence of flow behaviour around structured surfaces
Patterned steel sheets possess better material properties such as tensile strength, and bending strength as compared to plain sheets. Due to their known advantages, a series of laboratory experiments has been carried out in the International Graduate School (IGS) at BTU Cottbus-Senftenberg to investigate hexagonal structured sheet surfaces. In order to examine the possible application of structured sheets, aerodynamic properties and phenomena of structured plates need to be investigated: skin drag, pressure drag, vortex shedding, and boundary layers. In previous study projects, investigations were performed on the flow over structured surfaces (structured cylinders, plates and wind turbines). It was reported that the drag coefficient of the cylinder with patterns pressed outwards was found to be lower than the smooth cylinder by 65% [1] .While for the flat plate fig (1), the maximum reduction in shear stress coefficient was recorded for inwards structured surface of about 19% compared to the smooth surface [2, 3]. In the second phase of the study project, we will investigate flow behavior for enclosed flows such as channel flow and pipe flow.
Channel flow:
The channel flow is a turbulent flow conducted between two parallel flat plates. This type of flow is implemented in different applications such as the rectangular ducts used in heating, ventilation, and air conditioning (HVAC). The experimental investigation for the channel flow is conducted for Reynolds number Re = Ub d / ν (bulk velocity Ub, channel half-width d = D/2 ) ranging from 1.09 x 104 to 3.9 x 104 in wind tunnel of the aerodynamics and fluid mechanics department. The wind tunnel, Gottingen type, was designed for good performance up to bulk velocity 50 m/s with a background turbulence intensity less than 0.5% of the incident flow. Two parallel plates with a separation distance D = 50mm are mounted in the test section of the wind tunnel as shown in fig (2). The sides of the channel were closed using transparent acrylic side leading to span wise dimension at 11,9 D. The stream wise length measures 22,4 D. Three strips of tripping device sandpapers were used to trigger the turbulent boundary layer as in fig (3). All measurements were conducted in front and rear the tested sheets as shown in fig (3) using the Laser-Doppler anemometry. For computing the mean velocity of the local flow measurements at least 20,000 samples were acquired at every measuring positions. The experimental results show an agreement with the direct numerical simulation data (DNS) (fig.4) carried out in-house by A.Shahripour. Also the Friction coefficient was measured by different methods, in (fig.5) it is shown that the hexagonal inward structures decrease the friction coefficient up to 27 % compared to the smooth surface. In the second part of the research, we are going to measure the friction drag using static pressure measurements and investigate the hexagonal structures in form of the structural pipe segment in the Cola pipe facility.
Bibliography:
- Butt, U. & Egbers, Ch., 2013, Aerodynamic characteristics of flow over circular cylinders with patterned surface, Int. Journal of Materials, Mechanics and Manufacturing, Vol. 1, Nr. 2, 2013, pp 121-125
- Butt, U. , Experimental investigation of the flow over macroscopic hexagonal structured surface, Doctoral thesis, 2014
- Butt, U., Jehring, L., Egbers, Ch., 2014, Mechanism of drag reduction for circular cylinders with patterned surface, Int. Journal of heat and fluid Flow, Vol. 45, 2014, 128-134
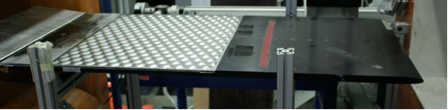
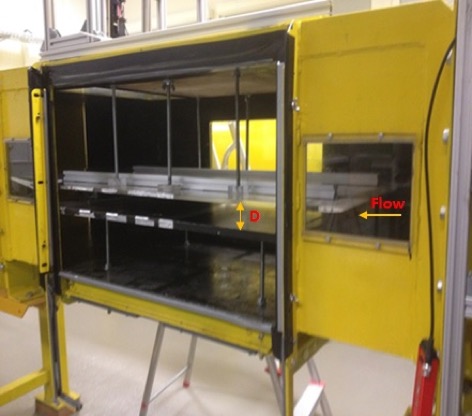
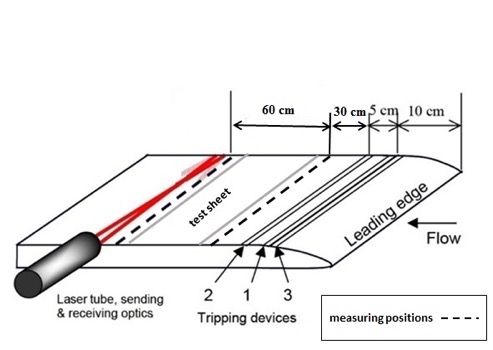
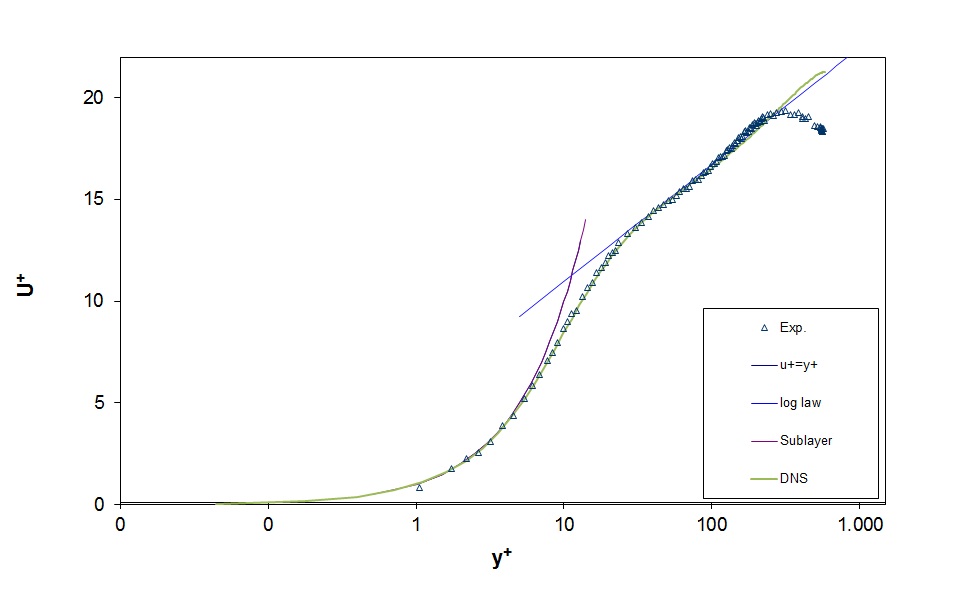
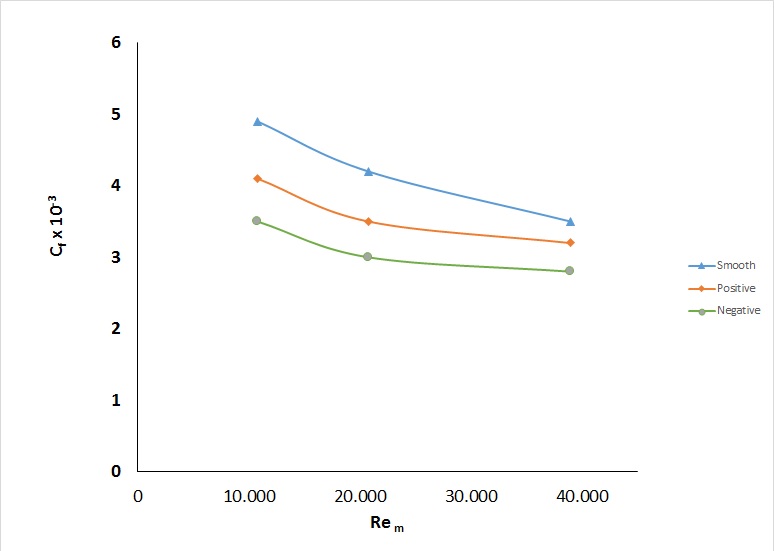