Eugen Julius Richard Dyckerhoff (1844 – 1924) Erfindungen und Forschungen
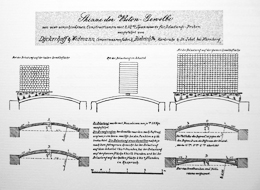
Nach dem Eintritt in die Firma Lang & Cie. war Eugen Dyckerhoff bestrebt die Qualität der dort hergestellten Produkte zu verbessern. Hierzu führte er systematisch Experimente durch. Bei seinen Forschungsarbeiten konnte er auf die Erfahrungen, die er im Forschungslabor von Dyckerhoff & Söhne gesammelt hatte, zurückgreifen. Darüber hinaus bereiste er mehrere europäische Länder um sich einen „Überblick über die neuesten Entwicklungen im Bereich der Betonproduktion zu verschaffen“ [STEGMANN 2009, S. 1372; aus dem Englischen durch den Verf. übersetzt]. Ein Ergebnis seiner Forschung war unter anderem, dass sich die Qualität des Betons erheblich verbesserte, wenn man während der Verarbeitung des Betons nur so viel Wasser und Zement hinzufügte, wie für die Verarbeitung notwendig war. Mit dem Prozess des Stampfens und damit einhergehend des größeren Eigengewichtes verbesserte sich die Festigkeit des Betons und dessen Neigung zu Schwindrissen wurde verringert. Gegenüber den erzielten Verbesserungen im Vergleich zum gegossenen Beton war der hohe Arbeitsaufwand, der benötigt wurde, um Bauteile herzustellen, nachteilig [KLASS 1965, S. 20]. Trotz der Entwicklungsarbeiten zum Stampfbeton ist davon auszugehen, dass Eugen Dyckerhoff nicht den Stampfbeton erfunden hat. Diese Annahme beruht auf einen Aufsatz in der Deutschen Bauzeitung von 1888 mit dem Titel „Über Betonbauten“, in dem Dyckerhoff berichtet, dass seines Wissens nach bereits Anfang der 1860er Jahre Stampfbeton für den Bau verschiedener Bauwerke verwendet wurde [DYCKERHOFF 1888a, S. 242].
Eugen Dyckerhoff beschäftigte sich nicht nur mit der Herstellung von Beton sondern auch mit dessen Verwendung bei Bauwerken. Sein Augenmerk richtete er hierbei besonders auf die Konstruktion von Gewölben, da sich hierbei eine Vielzahl von möglichen Anwendungsbereichen ergaben [STEGMANN 2008, S. 1]. Neben den unternehmerischen Gesichtspunkten war ihm auch daran gelegen, zu beweisen, dass das Material Beton für den Bau von Gewölben geeignet war. Besonders die Behörden standen dem Material noch kritisch gegenüber [STEGMANN 2008, S. 1]. Eugen Dyckerhoff verwendete bei seinen Experimenten „Bögen mit hohen Auflagerkapazitäten, wie sie schon in Frankreich produziert wurden“ [STEGMANN 2009, S. 1374; aus dem Englischen durch den Verf. übersetzt]. Hierzu führte er eine Vielzahl von Versuchen mit unterschiedlichen Lastannahmen durch, um zu ermitteln bei welchen Lasten die Bögen versagten [STEGMANN 2009, S. 1375]. Im Anschluss der Experimente veröffentlichte er seine Forschungsergebnisse [STEGMANN 2009, S. 1375]. Praktisches Ergebnis seiner Forschung war die Fußgängerbrücke auf der Gewerbe- und Kunstausstellung in Düsseldorf im Jahr 1880, bei der er die Eignung von Beton für den Bogen- und Gewölbebau aufzeigte. [STEGMANN 2008, S. 1-2; STEGMANN 2009, S. 1375]
Im Gegensatz zu gegossenem Beton besitzt Stampfbeton eine nur erdfeuchte Konsistenz. Um den Beton ausreichend zu verdichten, wird zunächst eine in der Regel 15-20 cm dicke Schicht in eine Schalung gegeben und mit zu Hilfenahme von Geräten, früher teils noch mit den Füßen, gestampft. Hierbei wird der Beton so lange gestampft, bis er eine geschlossene Oberfläche aufweist und zu „schwitzen“ beginnt, d.h. bis sich auf der Oberfläche eine dünne Wasserschicht gebildet hat. Anschließend wird der Beton ca. 1 Tag zum Erhärten „in Ruhe gelassen“. Ist die Schicht ausreichend erhärtet, kann die nächste Schicht aufgetragen werden. Um die Haftung der neu aufzutragenden Schicht zu verbessern, wird zunächst die vorhandene Schicht aufgeraut, gereinigt und befeuchtet. Während des Herstellungsprozesses bspw. eines Pfeilers ist auf die Einheitlichkeit und Geschlossenheit der jeweiligen Schichten zu achten, da die Gefahr besteht, dass sich Nester mit haufwerksporigem Gefüge in den Außenflächenbereichen bilden. Diese sind nachträglich nicht mehr rückstandslos zu beseitigen. Beim Bau kann es, wie es auch aus dem Lehmbau bekannt ist, zudem zu einer Vorwölbung der Schichten kommen. Eine Vorwölbung kann dann entstehen, wenn ein zu großer Druck beim Aufbringen der neuen Schicht erfolgt und gleichzeitig die darunter liegende Schicht noch nicht vollständig ausgehärtet ist. Diese Vorwölbung deutet meist auch auf einen minderwertigen Stampfbeton mit einer zu geringen Grundfestigkeit der einzelnen Schichten hin.
Bei Stampfbeton handelt es sich um ein unbewehrtes Baumaterial, welches zwar große Druckkräfte, jedoch nur bedingt Zugkräfte (etwa 1/10 der Druckkräfte) aufnehmen kann. Somit ähnelt Stampfbeton hinsichtlich seiner Eigenschaften denen von Naturstein. Der Beton weist eine nur geringe bis keine Schwundriss-Bildung aufgrund seiner nur erdfeuchten Konsistenz auf. Dazu trägt auch der hohe Grad der Verdichtung bei, die durch die stampfende Verarbeitung erzielt wird. Diese Verarbeitungsweise ist auch ein Grund für das größere Eigengewicht von Stampfbeton gegenüber gegossenem Beton. Stampfbeton kann monolithisch verarbeitet werden, da er weniger anfällig für Formveränderungen ist. Aufgrund dessen, dass Stampfbeton nur Druckkräfte aufnehmen kann, sind die Anwendungsbereiche meist auf Bogenkonstruktionen, Fundamente und untergeordnete Bauteile beschränkt. Wird er jedoch hinsichtlich seiner Eigenschaften korrekt verarbeitet, so können Bauwerke aus Stampfbeton sehr resistent und beständig sein, wie bspw. verschiedene noch in Betrieb befindliche Brücken bestätigen (Bsp. Illerbrücken von Kempten, 1904-1906).
Bei dem sogenannten „Walzbeton“ handelt es sich um eine Weiterentwicklung des Stampfbetons. Der Walzbeton ist in Deutschland wenig verbreitet. Häufige Anwendung findet er jedoch z.B. in den USA als „Roller Compacted Concrete“ im Straßenbau. Dabei wird er in Schichten von 18 bis zu 25 Zentimetern mit großen Straßenfertigern aufgebracht, vorverdichtet und mit schweren Glattmantel- oder Gummiradwalzen verdichtet. Ebenso wie der Stampfbeton kann der Walzbeton nur Druckkräfte aufnehmen. Deshalb ist die Voraussetzung für eine einwandfreie Betondecke eine einwandfreie Verdichtung des Untergrunds zur Ausbildung einer ausreichenden Tragschicht. Im Straßenbau wird häufig eine dünne Schicht von Gussasphalt nachträglich aufgetragen, die dem Höhenausgleich sowie einer besseren Befahrbarkeit der Oberfläche dienlich ist. Walzbeton stellt aber auch eine bewährte Lösung für die Herstellung von großen Hallenböden mit wenigen Fugen dar.
Anwendung fand Stampfbeton auch bei der Herstellung von „Stampfbetongewölbe“, eine Form der „Preußischen Kappen“. Dabei werden unbewehrte, gewölbte Platten für geringe Spannweiten neben einander angeordnet. Im Scheitelpunkt weisen sie eine Stärke von 8 bis 15 Zentimeter auf. Sie spannen quer zwischen Profilstahlträgern. Über diese erfolgt der Lastabtrag auf Stützen. Ab Mitte des 19. Jahrhunderts war diese Bauweise im Manufaktur- und Geschäftsbau Berlins sehr beliebt und weit verbreitet. Der Grund dafür war der einfache und zügige Einbau gegenüber der aufwändigen Schalung bei Gewölbedecken aus Hohlsteinen mittels patentierter Schalung, die unter die Stahlträger gehängt wurden. Des Weiteren waren deutliche Vorteile gegenüber den Holzbalkendecken in Bezug auf deren Beständigkeit (Fäule) und Brandschutz gegeben.